Lightweighting strategies inspired by birds
Reducing weight in all kinds of vehicles is currently one of the hot topics for Materials Science and Product Design. This goal is directly related to one of the grand challenges that society is facing, that is, mitigate greenhouse gases (GHG) emissions by reducing fuel consumption. Lighter vehicles consume less fossil fuels, which is definitely an effective way to reduce their carbon footprint. This is not a minor thing, being the transportation sector the second largest contributor to GHG emissions, only surpassed by the energy sector. Last year, emissions from cars, trucks, commercial aircraft, maritime transport and railroads made 27% of the total US emissions and 25.8% of the EU ones.
That’s why researchers and engineers are now paying much more attention to innovative ways of reducing weight in transport systems. The main strategies may seem obvious: either you change the materials that vehicles are made of, change their design, or both. However, solutions are not as obvious as it may appear at first sight. Guaranteeing optimal performance and safety is vital when talking about transportation. Solutions might have less weight, but they need to have the same performance, and that’s the real challenge for materials engineers and designers.
As in many other fields of science, experts are looking at how nature manages to design lightweight, high-performance materials. And in this regard, who knows better about a good weight/performance transport system than birds? This is the focus of a recently published article 1 in which birds’ wings are studied as an example of an extremely lightweight biological system. They focus on how evolution has developed the wing’s feathers and bones as a perfectly optimized structure for flight.
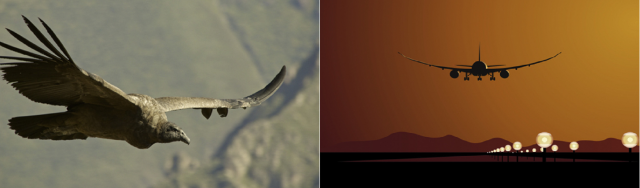
Birds, just like planes, can fly because wings’ skeleton and feathers act together to allow a high lift-to-weight ratio. This is achieved by two simple movements of the bird’s wing: the upstroke or recovery stroke, where feathers separate to allow the air flow through them to minimize downward forces, and the downstroke or power stroke, where flaps do not allow air through in order to maximize capture of air. As a result of these movements, which involve intense local loadings, wings’ bones and feathers are subject to strong bending and torsion moments. Through millions of years of evolution, these mechanical requirements have shaped the wing morphology.
Both wing’s bones and feathers share the same lightweight design premise: a thin, dense exterior combined with an almost hollow interior. Certainly, thick walls would add too much weight to the whole structure; but on the other side, thin walls could result in buckling and collapse. To avoid this from happening, nature provides two main strategies: lightweight, reinforcing internal structures and high density walls. In fact, birds have quite dense bones compared to other animals (2.15g/cm3). But let’s analyse bones and feathers separately.
The wing bones
The first characteristic of wing bones is that most of them are pneumatic, that is, they are not marrow-filled, but hollow. This feature not only provides weight reduction, but also increases skeletal buoyancy through its connection to the pulmonary system. To provide high mechanical strength, these hollow bones have thinner but denser walls than marrow-filled ones. In addition, wing bones present an interesting reinforcing strategy, as it can be seen in the image below. While there is a hollow, circular, mid-cross section, towards the end of the bone a peculiar set of struts appears acting as a reinforcing structure. These struts prevent the bone from collapsing under the influence of the in-flight forces.
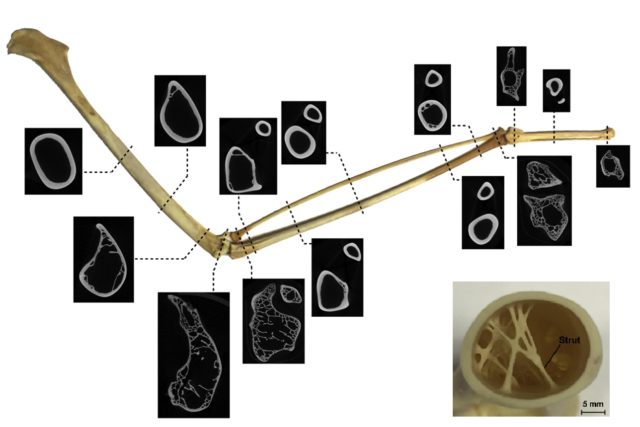
Regarding their composition, wing bones share the same raw material across all birds’ species, hydroxyapatite crystals. This material can be considered as a natural, fiber-reinforced composite whose fibers are hierarchically organized from the nanoscale to the macroscale, as shown in the picture below. As in many synthetic, man-made composites nowadays, bone’s fibers are directionally arranged to achieve maximum performance and stability. In the case of the bird’s wing, the bone must excel in resisting bending and torsion moments.

The flight feathers
The flight feathers support most of the area of the wing, as bones only reach half the distance between the shoulder and the wing tip. Figure 4 shows the structure of the feather, which basically consist of a central feather shaft and the surrounding feather vane. Obeying the same design premise than wing bones, the feather shaft has a thin, dense exterior with an almost hollow interior. Interestingly, the part of the feather shaft close to the bird’s body (calamus) has a circular cross-section and is completely hollow; but as we move towards the end of the feather shaft (rachis), this circular cross-section transitions into a rectangular one where the interior is no longer hollow, but filled with a lightweight, closed-cell foam, whose walls are also a foam, what it has been called “a foam within a foam” (see figure 5). This unique morphology provides great flexural and torsional stiffness without sacrificing lightness.
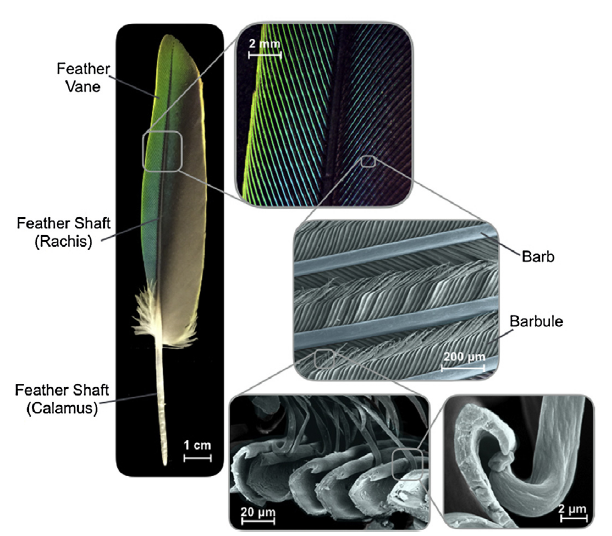
As for the feather vane, perhaps the most worth mentioning feature is that it is not a sealed structure, but contains channels through which air can flow. These channels open with the upstroke movement to allow air flow through them, and close with the downstroke movement in order to capture more air and promote the upward forces.
Regarding material composition, flight feathers are completely made of β-keratin and can also be considered as a fiber-reinforced composite with many levels of organization, from the nanostructure to the macrostructure. This composite design serves as an efficient material that allows the feather to be strong yet lightweight.
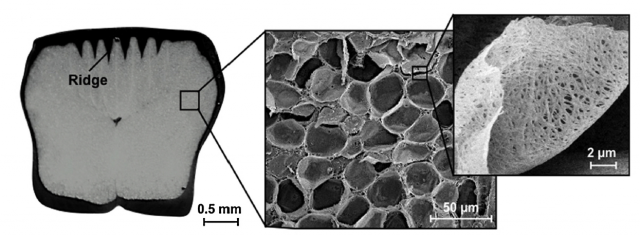
Of course, birds differ enormously in size and flight style. Think about a 2g hummingbird with a wingspan of barely 8cm, versus an 11kg Andean condor with a wingspan of at least 3 meters; or the different flight style of an eagle, which achieve flight by flapping and soaring, versus a seagull, which flaps and glides; or a duck, which can also dive and swim. While the above design premises are the same across species, they have different adaptations for specific environments. As an example, birds that are able to dive, like ducks, are an exception to the pneumatic bones rule. They have marrow-filled wing bones which maintain higher strength in impact and prevent excess of buoyancy while diving.
Have any of these features of birds’ wings inspired engineered structures or materials? The answer is yes, although this knowledge has not been fully used so far. We find examples of similar solutions in some torsion resistant structures such as torsion boxes in ship’s containers, which prevent the torsional bending caused by the movement of waves without adding excessive weight. We also find the characteristic struts of the wing bone applied to reinforce the ribs of some airplane wings. The flexible, composite wing of the Boeing 787, shown in figure 1, perfectly mimics the wing curvature of the Andean condor’s feathers, which provide efficiency and dampen turbulence. Finally, the changing cross-section of the feather shaft from a circular shape into a rectangular one is already inspiring the way in which earthquake-resistant buildings are designed.
So far, the main obstacle to take advantage of all this knowledge about the wing morphology has been the extreme difficulty to manufacture products with the same level of complexity as these natural materials. However, recent developments on smart manufacturing techniques, such as additive manufacturing, self-assembly or electrospinning, promise to be the definite impulse to enable us with the same freedom to design that nature enjoys.
References
- T. N. Sullivan et al. (2017) Extreme lightweight structures: avian feathers and bones Materials Today doi: 10.1016/j.mattod.2017.02.004 ↩
1 comment
i am looking for the cross specification of Condor, Stork, Eagle of the wing. I cannot find these anywhere. Have You coordinates (x,y values) table like Seliger, X.Wortmann, Eppler?
I am a glider pilot.