Recent advances in lithium-ion rechargeable batteries
Lithium-ion batteries are widely used in portable electronic devices and electric vehicles since their introduction by Sony in 1991. Safety is an important concern since about two billion cells are produced every year but with a one-in-200,000 failure rate. Excessive temperature variations and high temperatures over the melting point of the metallic lithium can cause a thermal runaway reaction that ignites a fire and consequently cause a violent explosion. To avoid the inherent instability of lithium metal, non-metallic lithium batteries are preferred, but at the price of a lower energy density. However, in some cases Li dendrites form, leading to severe short circuiting. Hitoshi Maruyama, from University of Tsukuba, Ibaraki, Japan, and colleagues 1 have proposed a new anode material that minimizes dendritic Li formation; concretely, they have suggested the use of three-dimensional amorphous silicon polymers poly(methylsilyne) and poly(phenylsilyne) for the anode. Both exhibit an excellent performance in thermal-abuse tests.
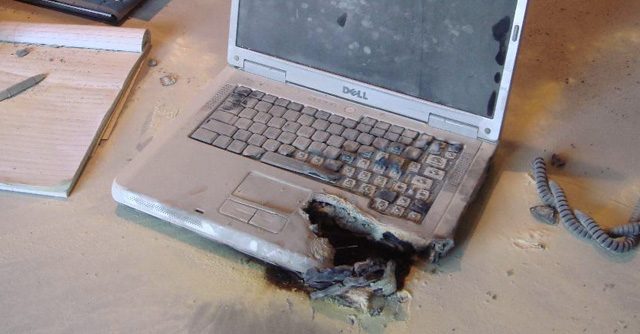
Polysilynes and polysilanes are organosilicon polymers with the formula (RSi)n and (R2Si)n, resp., with R = alkyl or R = aryl. Maruyama et al. have used both R = methyl and R = phenyl, as shown in Figure 1 (a). These polymers exhibit a strong Li ion absorption, even at low-temperature, with a very low Li compound formation. The results suggest that polysilynes are better for the anode material than polysilanes. They absorb Li ions by means of a redox reaction and, due to their polymeric silicon structure, have a Li ion mobility in the anode higher than that in a graphite anode. For Li-ion batteries operated at low temperatures or high rates, they show an extraordinary stability. As usual, future studies are planned to further develop the design of the Si framework and to optimize the organic substituents in order to increase the performance.
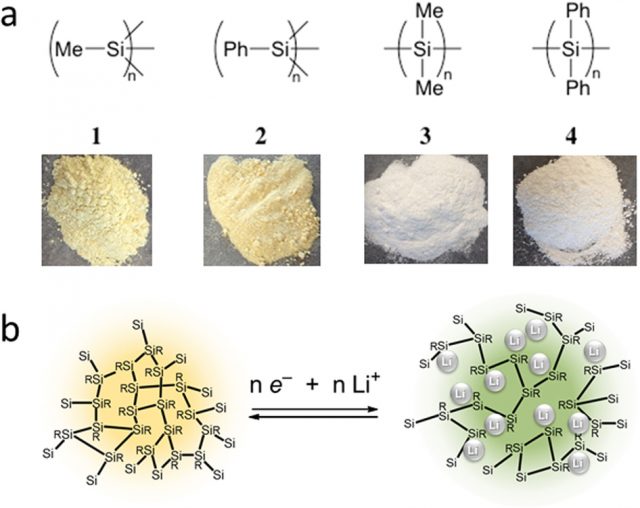
The operating temperature of Li-ion batteries must be well controlled, as its performance, health, cycle lifetime, and safety depends on it. The implementation of efficient cooling systems requires an understanding of the temperature effects on the degradation rate of each component. Feng Leng, Nanyang Technological University, Singapore, and colleagues 2 study the performance degradation rate for each component in a Sony Li-ion battery operating at different temperatures from 25 to 55 °C using a recently developed electrochemistry-based electrical model. Figure 2 shows the maximum charge storage capacity (Qm) as a function of temperature and cyclic aging. As the operating temperature changes from 25 to 55 °C, the degradation rate of maximum charge storage after 250 cycles is found to increase from 4.22% to 13.24%, and, as expected, Qm gradually decreases with an increasing number of cycles. The analysis of the results using the electrical model shows that the formation and modification of the surface films on the graphite electrode, as well as structural/phase changes of the LiCoO2 electrode, are found to be the main contributors to the increasing degradation rate of the maximum charge storage of Li-ion batteries with temperature.
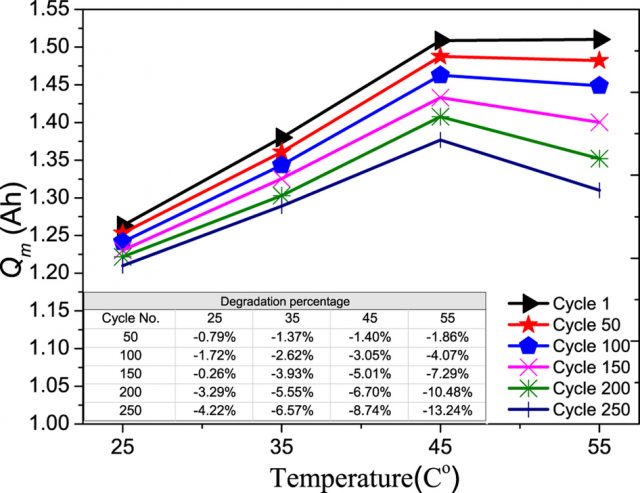
Degradation during cycle lifetime is the biggest problem for new designs of Li-ion batteries. For example, the use of aluminium as anode material promise low cost, high theoretical capacity, high electrical conductivity and so on, but the practical performance of Al-Li electrodes is poor due to several damage mechanisms; in fact, they are exacerbated by aluminium’s ~100% volume expansion/shrinkage during lithiation/delithiation. A promising solution to this problem is the use of a yolk-shell nanocomposite of aluminium core (30 nm in diameter) and TiO2 shell (~3 nm in thickness), as shown by Sa Li, Massachusetts Institute of Technology, Cambridge, MA, USA, and colleagues 3. The main problem of these nanocomposites is their industrial scale fabrication technique. The new paper reports a one-pot synthesis method (Figure 3) that is simple, cheap, scalable and uses only Earth-abundant elements (Al, Ti, O, H, C and S). The entire process is industrially scalable with minimal infrastructure requirement and fully compatible with current technology for battery assembly; therefore, it can be used for mass production.
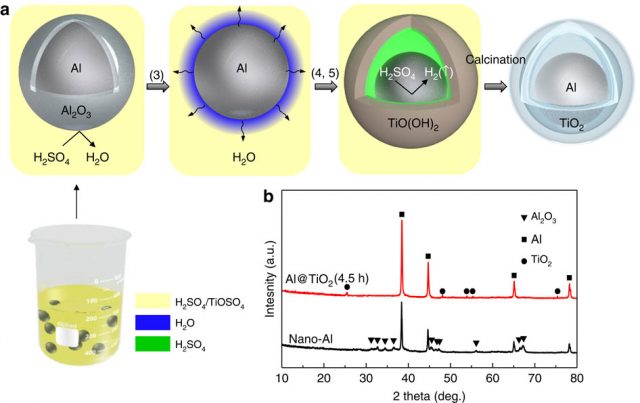
Figure 4 shows scanning electron microscope images of the Al@TiO2 yolk-shell particles. The aluminium nanoparticle about 30–35 nm in diameter, are encapsulated by the TiO2 shell, with well-defined void space in between that can accommodate the volume expansion. The complete coverage of TiO2, although only a few nanometres thick, is crucial to protecting the chemically active aluminium. The resulting Al@TiO2 (ATO) yolk-shell nanocomposite exhibits remarkable battery performance, with a long cycle life and an admirable rate capability.
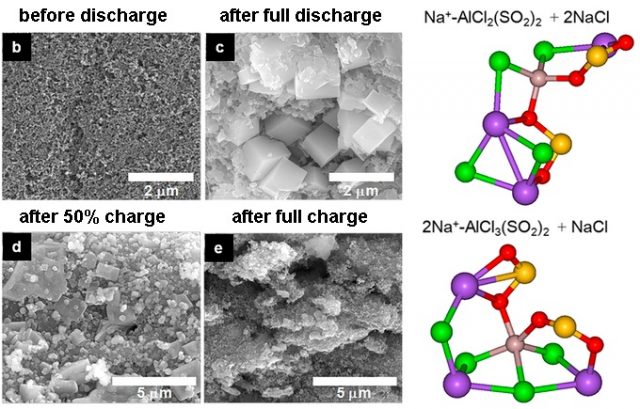
Non-flammable materials, like sodium, are an excellent alternative to Li-ion rechargeable batteries from the point of view of safety; however, there is a need to further improve their battery performance and cost-effectiveness for practical use. Goojin Jeong, Korea Electronics Technology Institute, Seongnam, Korea, and colleagues 4 have developed a new type of room-temperature and high-energy density Na–SO2 rechargeable battery. Its discharge capacity of 153 mAh/g, with an operating voltage of 3 V, and its cycle performance over 300 cycles, are very attractive features over other Na rechargeable batteries. However, these numbers need some improvements in order to be a promising candidate for the next generation energy storage system.
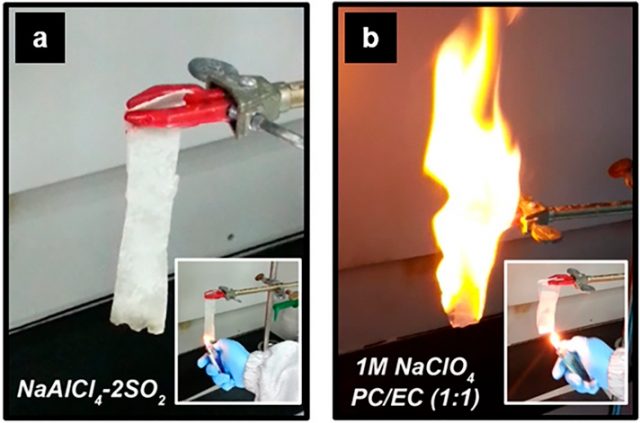
Na–SO2 rechargeable battery systems solve the main safety concern of other room-temperature Na-ion or Na–O2 batteries, they used flammable organic solvents. The Na–SO2 battery is nonflammable, even in direct contact with an open flame (Figure 6). Another important feature of a Na–SO2 battery stems from the still high Na+ conductivity of NaAlCl4⋅2SO2 at low temperatures (even down to–20 °C). However, further studies for fundamental understanding of a Na–SO2 battery are required to clarify the detailed reaction pathway during charge of the battery.
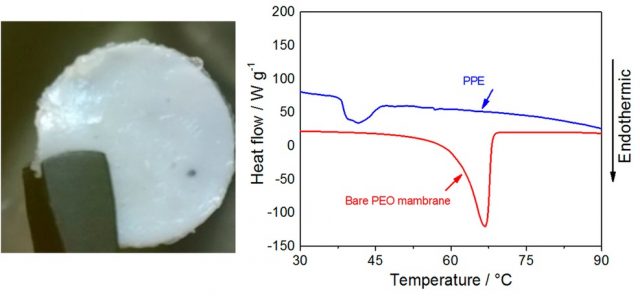
In terms of energy density Lithium-air batteries have no competence. Hence, several research lines are focused in the solution of its flammability risks and associated safety issues. The use of polymer electrolytes is very promising. Elia and Hassoun, both at Sapienza University, Rome, Italy, proposes a Li-O2 battery employing a plasticized, polyethyleneoxide (PEO)-based solid electrolyte, referred to as PPE 5. Their remarkable safety is due to the solid configuration of the electrolyte and the absence of volatile and flammable components. Figure 7 (left) shows a photographic image of the solid shape. As shown in Figure 7 (right), the typical endothermic peak at about 65 °C (see PEO curve), associated to the polymer melting and corresponding conductivity increase, shifts to about 40 °C by the plasticization process. However, the PPE curve is always over the PEO curve, even at the shifted peak, so the battery has a high safety level due to its solid polymer configuration.
The new polymer configuration lithium-oxygen battery has a theoretical energy density of the cell of 1350 Wh/kg, a high value compared to the conventional lithium-ion battery cathodes, typically ranging from 600 to 700 Wh/kg. Further cell optimization can result in practical energy densities near twice of the conventional lithium ion batteries and longer cycle lifetimes.
In summary, the search of the perfect battery that will make electric cars practical is currently very active. Lithium-ion battery biggest weakness is its tendency to become unstable if it is overheated, overcharged or punctured. Researchers are trying different approaches to solve the problem without degrading its performance. Safety is the main concern in automobile applications since traffic collisions cannot be avoided.
References
- Hitoshi Maruyama et al., “Improving battery safety by reducing the formation of Li dendrites with the use of amorphous silicon polymer anodes,” Scientific Reports 5: 13219, 07 Aug 2015, doi: 10.1038/srep13219. ↩
- Feng Leng et al., “Effect of Temperature on the Aging rate of Li-Ion Battery Operating above Room Temperature,” Scientific Reports 5: 12967, 06 Aug 2015, doi: 10.1038/srep12967. ↩
- Sa Li et al., “High-rate aluminium yolk-shell nanoparticle anode for Li-ion battery with long cycle life and ultrahigh capacity,” Nature Communications 6: 7872, 05 Aug 2015, doi: 10.1038/ncomms8872. ↩
- Goojin Jeong et al., “A room-temperature sodium rechargeable battery using an SO2-based nonflammable inorganic liquid catholyte,” Scientific Reports 5: 12827, 05 Aug 2015, doi: 10.1038/srep12827. ↩
- Giuseppe Antonio Elia, Jusef Hassoun, “A Polymer Lithium-Oxygen Battery,” Scientific Reports 5: 12307, 04 Aug 2015, doi: 10.1038/srep12307. ↩
4 comments
[…] contribución “Recent advances in lithium-ion rechargeable batteries,” Mapping Ignorance, 02 Sep 2015, cuyo primer párrafo (en inglés) dice: “Lithium-ion batteries are widely used […]
[…] example of this collaborative approach is illustrated in this this recent article about lithium-ion rechargeable batteries: One of the articles cited include researchers from […]
There is an failure in paragraph 2, when you refers to R = methyl and R = phenyl , saying that this is shown in figure 1, but it´s shown in figure 2.
Thanks, Antonio.