Carnivorous plants inspire novel liquid repellent surfaces
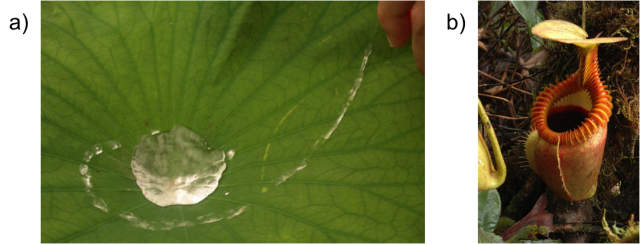
Natural non-wetting structures, particularly lotus leaves (Fig. 1a), have inspired the development of synthetic liquid-repellent surfaces. These surfaces rely on the formation of a stable air–liquid interface, but present limited repellency to oils with high contact angle hysteresis, failure under pressure and inability to self-heal. The paper by Wong et al. 1 presents a novel approach inspired by Nepenthes pitcher plants (Fig. 1b).
These plants use their microtexture structures to lock-in an intermediary liquid that acts itself as a repellent surface. The liquid surface energy, combined with the roughness of the plant surface, creates a highly stable continuous film. Then, when an insect steps on the film, it repels the oils on their feet and the insect slides down to the bottom where the digestive juices are. Using this idea, Wong et al. have developed a synthetic liquid-repellent surface or SLIPS (slippery liquid-infused porous surface). It mainly consists of a film of lubricating liquid locked in place by a micro/nanoporous substrate. The liquid surface provides immediate self-repair to damages in the fully-wet underlying substrate, is largely incompressible, and can be chosen to repel any immiscible liquids.
SLIPS could be helpful in fluid handling and transportation applications, optical sensing, medicine, and as self-cleaning and antifouling materials operating in extreme environments.
It is commonly known that, due to surface tension, liquid droplets tend to minimize their surface adopting a spherical shape. However, when in contact with a surface, the liquid is spread across the surface due to adhesive forces. The wettability of a surface, which can be measured by the contact angle between the liquid–vapor interface and the solid–liquid interface (Fig. 2), depends on the surface structure and the liquid surface tension. So, surfaces with a contact angle < 90° are called hydrophilic and those with an angle >90° are called hydrophobic.
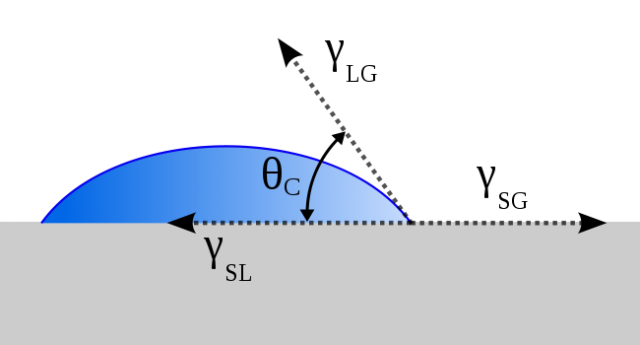
Hydrophobicity is of great importance to plants, which use it as a protection against fungi or algae, and to prevent the contamination of the area exposed to light, which would compromise photosynthesis. On the other hand, some animals and insects use hydrophobicity to cleanse their body parts.
The traditional approach: the Lotus effect
The development of liquid-repellent surfaces is currently inspired by the so-called lotus effect. This effect is based on the hydrophobic double structure of the surface, which consists of an epidermis with numerous papillae (10 to 20 µm high, 10 to 15 µm wide) covered by a water-repellent layer of waxes.
Plants like the lotus can reach a contact angle of 170° -they are called superhydrophobic- so a droplet’s contact area is only 0.6%. So, when a water droplet rolls across a contaminated surface the adhesion between the dirt particle and the droplet will be higher than that between the particle and the plant surface, and the droplet will remove all dirt. However, this self-cleaning effect is based on the high surface tension of water and therefore it does not work with any liquid solvent. Other limitations of the lotus-based surfaces are their inability to withstand high pressures or impacts, which occur commonly in driving rain or in underground transport pipes. Moreover, these synthetic surfaces are prone to irreversible defects arising from mechanical damage and fabrication imperfections.
The new approach: SLIPS (slippery liquid-infused porous surface)
The syntethic surfaces developed by Wong et al. are conceptually different from the traditional lotus-based surfaces. Inspired by Nepenthes pitcher plants, they use nano/ microstructured substrates that lock in place the infused lubricating fluid (Fig. 3a).
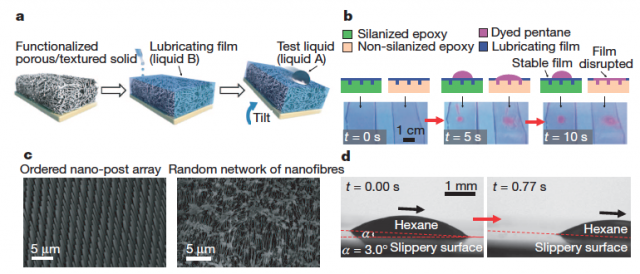
Two types of porous solids were tested to generate roughness (Fig. 3c), namely periodically ordered and random arrays of nanoposts functionalized with a low-surface energy polyfluoroalkyl silane, and a random network of Teflon nanofibres distributed throughout the bulk substrate.
For the lubricating film, they used low-surface-tension perfluorinated liquids, which are non-volatile and immiscible with both aqueous and hydrocarbon phases. This way, the liquid is able to form a stable, slippery interface with the solid substrates for a broad variety of liquids (Fig. 3d and Fig. 4a, b).
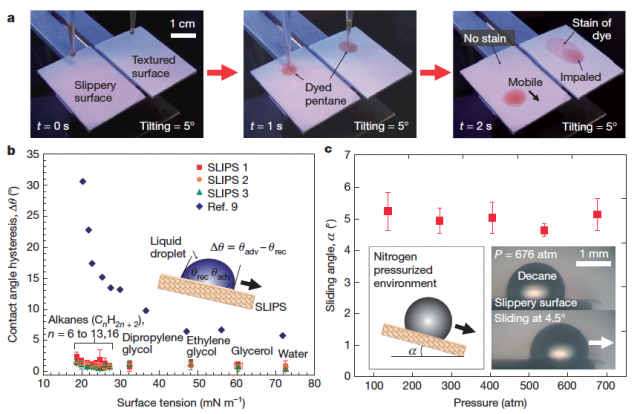
To generate the surfaces, the liquid was imbibed into the porous substrates, obtaining a very smooth surface with a roughness of about 1 nm.
SLIPS were tested with liquids of surface tension ranging from (n-pentane) to (water), measuring contact angle hysteresis (difference between the advancing and receding contact angles of a moving droplet), and sliding angle (surface tilt required for droplet motion), which directly characterize resistance to mobility. Very low values of both magnitudes were obtained, hence confirming a lack of pinning, consistent with a defect-free surface with extreme liquid repellency.
Besides this, SLIPS are insensitive to texture geometry: the lubricating film confers liquid repellency to the configuration, while the porous substrate immobilizes the film.
Also, the smoothness of the liquid–liquid interface eliminates the dependence of the contact angle hysteresis with surface tension, which is very significant in lotus-leaf-based surfaces.
When tested in different ambient pressures (Fig. 4c), SLIPS have been capable to repel water and liquid hydrocarbons with pressures up to 676 atm.
As mentioned before, the lubricating film also confers to the surface the property of self-healing after damage of the porous material by abrasion or impact. Basically, the liquid flows towards the damaged area by capillarity, and refills the voids (Fig. 5a). Even with extensive damage, SLIPS are capable to restore their liquid repellency function (Fig 5b).
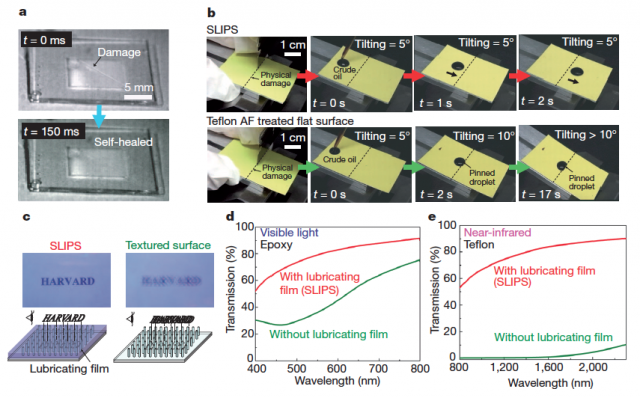
SLIPS can be made optically transparent by choosing substrate and lubricant materials with matching refractive indices, (Fig. 5c–e). This is a very challenging property for hydrophobic surfaces, since they require nanostructures with dimensions under the sub-diffraction limit (< 100 nm); and the large difference in refractive index at the solid–air interface results in significant light scattering that reduces light transmission.
Further tests have been carried out with more complex fluids that wet and stain most existing surfaces, such as crude oil (Fig. 6a) and blood (Fig. 6b), with ice (Fig. 6c), and even with insects (Fig. 6d), proving the versatility of SLIPS.
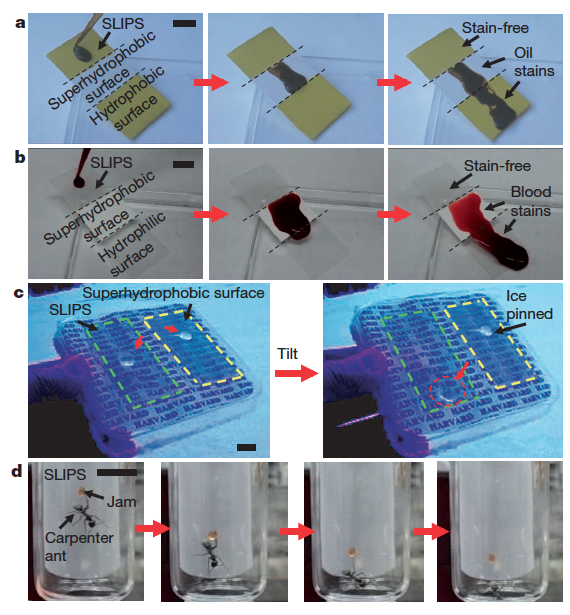
Of course, all these capabilities of SLIPS could be compromised if the lubricant evaporates or is dragged due to shear under high flow conditions. So it is necessary to choose a lubricant with a minimal evaporation rate, and enhanced viscosity, or simply to integrate the SLIPS with a fluid reservoir that ensures long operation life.
Conclusions
A new approach based on the Nepenthes pitcher plants has been developed to generate liquid repellent surfaces. Unlike the traditional surfaces, which are based on the lotus effect, SLIPS exhibit negligible contact angle hysteresis and low sliding angles for liquids with a broad range of surface tension values and complex mixtures, quick self-healing, extreme pressure stability and optical transparency. All these advantages, together with an easier and cheaper manufacturing process, make SLIPS a very promising tool.
References
- Wong, Tak-Sing, Kang, Sung Hoon, Tang, Sindy K. Y., Smythe, Elizabeth J., Hatton, Benjamin D., Grinthal, Alison, Aizenberg, Joanna (2011). Bioinspired self-repairing slippery surfaces with pressure-stable omniphobicity. Nature 477, 443-447. ↩
1 comment
[…] Carnivorous plants inspire novel liquid repellent surfaces […]