Stuck like a gecko
We all know the story of that Swiss engineer who came up with the hoop-and-loop fastener system (also known under the brand name Velcro) just by paying attention to the burdock burrs stuck in his clothes and his dog’s fur after a walk in the Alps. When he put these burrs under the microscope a number of “hooks” were revealed, a perfect way for this plant to spread its seeds with the help of the passers-by.
Examining how nature solves complex problems has always been a clever starting point for materials scientists, and this bioinspiration specially applies to the field of adhesion. Adhesion is mainly a superficial phenomenon consisting of two dissimilar surfaces clinging to one another. The complexity of this problem varies depending on the chemistry and roughness of these surfaces and the kind of adhesion that we want to achieve (permanent or temporary, strongly attached or easily removable). But it has been a long time since scientists found in nature an exceptional example to mimic, that is, the gecko adhesion mechanism.
Geckos are very well known for sticking to almost every surface, even glass or Teflon, in a vertical or inverted manner, with an easy release and without damaging the surface in any way. It seems obvious that this extraordinary property has been the subject of many researchers in the field of adhesion, but it was not until 2000 that a consistent explanation was given by professors Kellar Autumn and Robert Full 1.
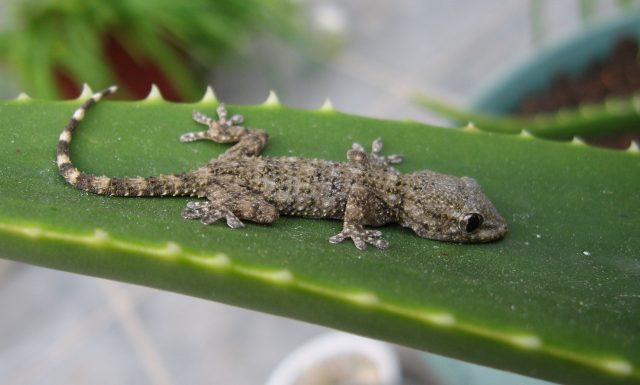
Autumn and Full discovered a sophisticated hierarchical structure in the gecko toe-pads: at the mesoscale an array of lamellar flaps, also known as scansors, are responsible for the large-scale adhesion (figure 2b). These flaps consist of stiff tendon tissue just covered by the surface skin. At the microscale, these scansors present a great number of setae (figure 2c and 2d) which in turn end in hundreds of fibrillar branches with spatular tips in the range of the nanoscale (figure 2e). This finding has allowed researchers to talk about a phenomenon of nanoadhesion, governed by van der Waals forces.
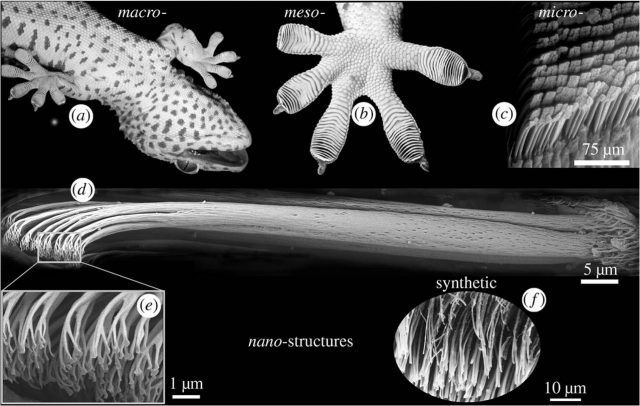
Most of the efforts carried out to mimic the strong adhesive capacity of geckos have been oriented to reproduce this nanofibrillar structure with synthetic setae (figure 2f) made out of polymers such as polyimide, polypropylene or even using carbon nanotubes. However, this approach still presents several drawbacks, the most important of them being the difficulty of their manufacture, the limited reusability of these nano-sized fibrils and the modest results in terms of adhesive force capacity achieved on “real surfaces”.
A new interesting approach to this problem of producing gecko-like adhesives has been recently published by researchers from the University of Massachusetts 2. The novelty of their study lies in the fact that, unlike many other previous works, it doesn’t focus on the nano-fibrillar structure of the gecko’s toe-pads, but in the system formed by these surface pads together with the tendon tissue system behind them. According to this approach, gecko’s strong adhesive capacity is due to the stiffness of the sub-surface structure, which allows a large-scale adhesion in a wide range of surfaces, and the softness of its skin, which conforms to the surface micro-topography, no matter how smooth or rough it is.
Keeping this concept in mind, a new adhesive material has been developed consisting of a soft elastomer pad, which provides the necessary softness to create intimate contact with a wide variety of surfaces in the range of micron or smaller scales, and a stiff fabric made out of woven carbon fiber integrated in this elastomer pad, acting as the characteristic tendon system of gecko feet and toes, responsible for the large-scale adhesion.
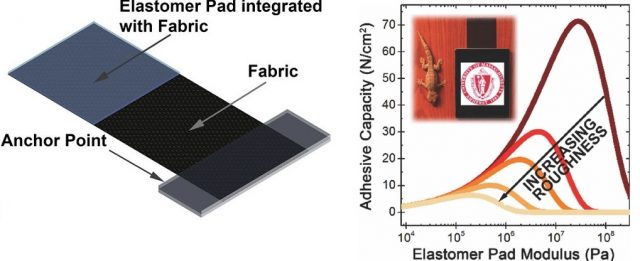
This new adhesive has been created on the assumption that the key scaling parameter governing the adhesive force capacity is, where A is the contact area between the two surfaces involved, and C is the compliance in the loading direction. Thus, a real good adhesive should be soft enough to maximize the contact area with the substrate, and at the same time stiff enough to distribute shear forces across a large area minimizing elasticity effects.
The resulting composite material is a combination of a low modulus polyurethane (ranging from 0.3 to 3 MPa) and a high modulus carbon fiber fabric (40 GPa) easily adaptable to different sizes and surfaces. For each specific surface roughness there is an optimum elastomer modulus in which the adhesive capacity reaches its maximum value (figure 3) and, as the roughness of the substrate increases, this maximum is shifted to lower elastomer modulus, thus allowing the necessary softness required to conform to the surface topography.
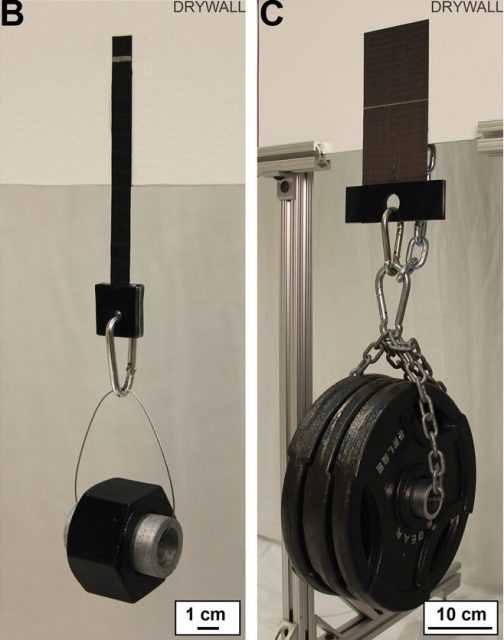
Obtaining reusable adhesives with high adhesive force over repeated cycles together with an easy release is quite a challenging task. The results for this new material are very promising, not only regarding the adhesive forces achieved, but also due to its ability to maintain these forces in different scales (figure 4) and in a wide variety of surfaces, from the smoothest (glass, teflon) to the roughest ones (painted drywall, concrete stone, wood).
All in all, it seems that mimicking the way in which nature manages to solve complex problems is anything but unique, and it is largely dependent on how we interpret what we see and where we turn the spotlight. In the field of materials science it is particularly important to successfully follow the path from the lab bench to market, and that means feasible, efficient and cost-effective materials. That’s why this new gecko-like adhesive seems a very good example of well-oriented bioinspiration directly applied to “real world” adhesion problems.
References
- Autumn K., Liang, Y.A., Hsieh, S.T., Zesch, W., Chan,W-P.,Kenny, W.T., Fearing, R. and Full, R.J. (2000), Adhesive force of a single gecko foot-hair, Nature, Vol. 405,pp. 681–5. ↩
- King D.R., Casey A. Gilman, Duncan J. Irschick & Alfred J. Crosby (2014). Creating Gecko-Like Adhesives for “Real World” Surfaces, Advanced Materials, n/a-n/a. DOI: http://dx.doi.org/10.1002/adma.201306259 ↩