Biological solutions for architectural problems
Materials science is becoming more and more an interdisciplinary field in which almost every traditional subject has its say. Disciplines such as biology, medicine, computational design, architecture or even music, painting or sculpture converge on this open-minded host. As a result, new inspiring research is coming from so many different fronts, brought together by their dealing with the fundamentals of matter.
One of these stimulating fronts comes from the concurrence of architecture and biology. A thorough understanding of biological systems and their structural behavior has proved a good start for coming up with new architectural concepts and proposals. As a matter of fact, some fundamental principles of natural load-bearing systems strongly differ from those of the usual architectural practices. For instance, whereas natural constructions are characterized by their material continuity, achieving a perfect integration of functionality, geometry and materiality, our buildings traditionally consists of a number of discrete elements, each performing a different function, leading to a material discontinuity in which parts’ assembly becomes particularly challenging due to difficult joints, mechanical stress peaks and similar issues.
In an attempt to mimic this material continuity of living systems, an interdisciplinary team of biologists, architects, engineers and computer designers have developed an exceptional lightweight, seamless and self-supporting pavilion made of a combination of glass and carbon fibers pre-impregnated with epoxy resin1.
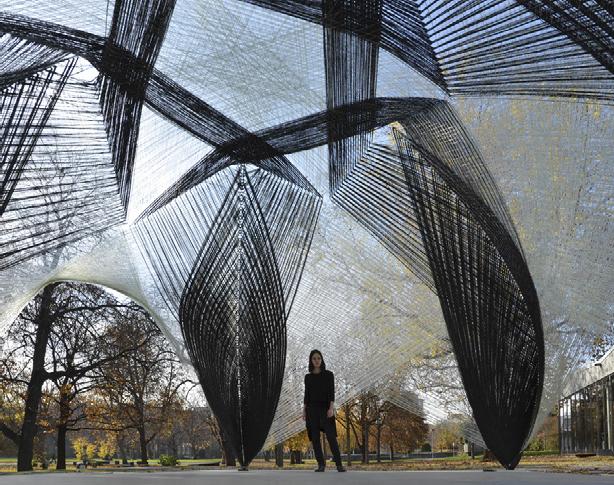
The biological system chosen as a role model in this study is the exoskeleton of the American Lobster (homarus americanus), a natural lightweight fiber composite very well known for its excellent mechanical strength and functional versatility. Once the morphological principles governing this structure has been identified they can be transferred into a technological application by means of a computational design process in which material science, structural engineering, architectural design and robotic fabrication work together to obtain a full-scale structure.
But, which are these principles governing the architecture of nature? Biologists have identified some of these guidelines common to most natural constructions: hierarchy, consisting of highly organized structures on multiple levels, from the molecular level to the macroscale; anisotropy, a wise alignment of material properties to achieve the best performance at a minimum material cost; heterogeneity, differentiating their elements according to functional adaptations and multifunctionality, some parts serving both physiological and structural purposes.
The exoskeleton of the American Lobster presents all these excellent features to serve as a role model for architectural new concepts. Starting from the monomeric saccharide units that conform the subsequent chitin polymer, a chitin-protein nanofiber-like system is obtained, later organized into sheets that rotate around a normal axis achieving a helical structure continuously varying in height, composition and fiber orientation according to its final function.

In order to replicate this complex natural system, the authors chose a robotic filament winding process of glass and carbon fibers, previously impregnated with an epoxy resin which would be later subjected to a temperature curing process. It is noteworthy that, while extensively used in many other fields of materials production, polymer composites still don’t have a wide presence in buildings’ construction apart from timid attempts in contemporary architecture; on the contrary, ancient technologies such as fired clay brick prevail over new materials perspectives. As a material group, polymer composites offer unquestionable advantages for architectural purposes: they are cost effective, easily repeatable through moulding techniques, lightweight but with a high strength/weight ratio. They also have excellent durability and corrosion resistance, and last but not least, they are easily reinforced with fibers leading to exceptional mechanical properties and anisotropic effects.
In the present construction, the combination of glass and carbon fibers responds not only to aesthetical considerations (the glass fibers provide a more appealing appearance) but also to structural and fabrication concerns. The higher elastic modulus of carbon fibers is suitable in those areas where mechanical reinforcement is required, while the more flexible glass fibers allow bigger deformations in strategic parts in order to reduce stress in the overall structure.
Of course, translating the design strategies of nature into a full-scale architectural prototype involves the development of appropriate digital tools for simulation and optimization of the resulting structure. These tools will allow exploring multiple design variations according to the initial boundaries, which are, on the other hand, constantly enriched by new empirical data and accommodated to the results obtained during the whole computational process.
The final structure of the pavilion is the result of three different simulation models working concurrently: the first one, a geometric representation model, is responsible of the overall size and appearance of the pavilion; the second one, an iterative winding simulation model, simulates the logical sequence in which the fibers have to be positioned in a single layer according to the desired mechanical response; finally, a global material simulation model helps to analyze multiple geometric surfaces detecting unsuitable parameters configurations. All the simulation processes are repeated until a satisfactory solution is obtained, not only in terms of structural performance, but also with regard to the architectural and aesthetic value of the full-size construction.

The next step will be to transfer the simulation results into a robotic fabrication setup, a crucial stage in which the reference to the biological role model has to be taken into account. The robot will have to carefully follow the previously defined syntax in order to achieve a consistent bond between the different layers of glass and carbon fibers, properly changing the orientation of each layer as it was found in the exoskeleton of lobsters. The authors also developed a simulation of the robot tool path in order to identify possible collisions, singularities, out-of-reach positions and so forth. The robot consisted of a 7-axis arm, constrained to a vertical plan of operation, as it is shown in the picture below.
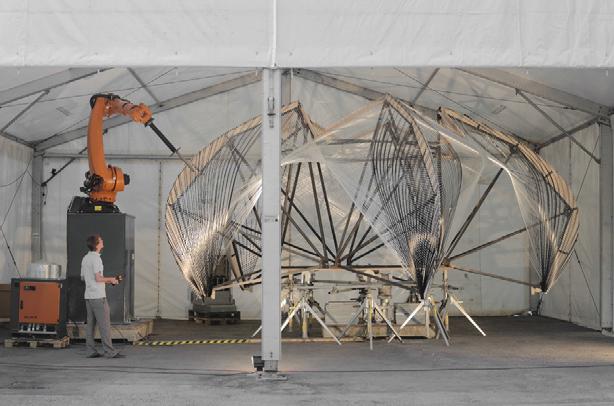
The overall structure, fabricated in 130 hours, results in a really aesthetically appealing pavilion. It is a clearly defined closed architectural space 4 meters high and 8 meters long, with 3 open entrance areas and an impressive thickness of just 4 millimeters. As for the whole weight, 60 kilometers of glass fibers and 30 kilometers of carbon fibers together with the epoxy resin give a total weight of 320 kilograms.
The design methodology developed in this interesting project offers a perfect example of collaborative research and the amazing possibilities yet to come in this field. The development of bigger architectural structures from this new perspective will be the real challenge for future experiments.
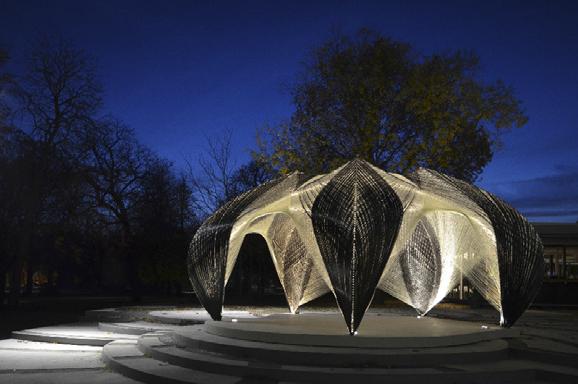
References
- Reichert S., Riccardo La Magna, Frédéric Waimer, Jan Knippers & Achim Menges (2014). Fibrous structures: An integrative approach to design computation, simulation and fabrication for lightweight, glass and carbon fibre composite structures in architecture based on biomimetic design principles, Computer-Aided Design, 52 27-39. DOI: http://dx.doi.org/10.1016/j.cad.2014.02.005 ↩