Real-time tracking of mesoscale surface oxidation changes
We are all familiar with rust. Rust is an iron oxide, usually red, formed by the reaction of iron and oxygen in the presence of water or air moisture, and it is a clear sign of metal corrosion by oxidation.
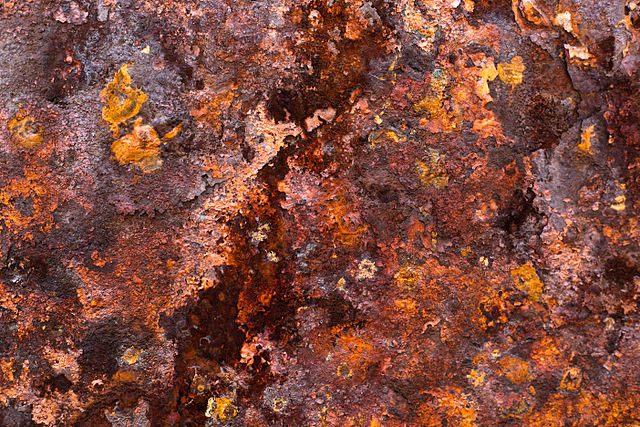
Oxidation is a ubiquitous phenomenon that proceeds via the electrochemical interaction of ambient oxygen molecules with atoms of the metal. The rate of formation of the oxide (or oxides) decreases as the thickness of the oxide film grows; therefore, the steady-state thickness of the oxide is determined by its transparency to penetration by oxygen molecules. The formation of a dense film (for example Al2O3 in aluminium) promotes surface passivation. Loose oxide films (Fe2O3 in iron or CuO in copper) hinder further oxidation, thereby facilitating surface corrosion.
Fundamentally, the oxidation of metal surfaces represents a remarkably complex reaction scenario at the solid-gas interface, in which heterogeneities at the surface as well as the supply and transport of the reacting surface species, are decisive ingredients. In the course of metal oxide formation, the metal-metal bonding is replaced by metal-oxygen bonding, a process which depends heavily on temperature and that determine the reaction rate at low temperatures.
In any general chemistry textbook, we can find a description of the initial microscopic processes in the oxidation of a metal surface. On the other hand, in any engineering materials textbook we will find a general description of macroscopic rates of corrosion and methods to prevent it. But what we would not find in any of them is a description of the mesoscopic scale processes, those that include the roughening and patterning of the surface. This information is critical if we are to understand catalysis properly; even more if we consider that recent studies hint that metal oxides could be more active than the current metal catalysts.
To achieve this what is needed is a non-destructive laboratory method that would allow to map the mesoscale surface morphology and structure on a few nanometer scale. This is exactly what a group of researchers, including Ikerbasque’s Eugene Krasovskii of the Materials Physics department (UPV-EHU) and DIPC, has provided1 with a proof-of-principle testing of the oxidation of a ruthenium surface at high temperatures using intensity-voltage low energy electron microscopy, I(V)-LEEM. This approach, when combined with state-of-the-art theoretical models built from ab initio scattering theory, yields a real-time structural identification in a reactive environment. The results are published in ACSNano.
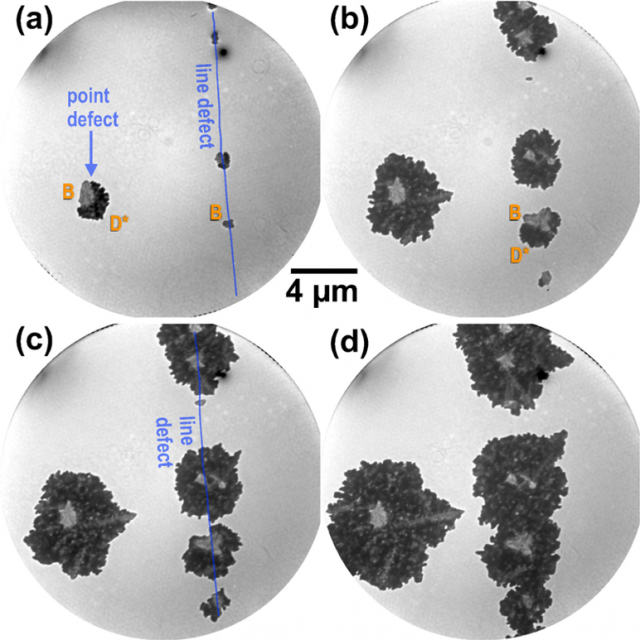
The authors focused on the oxidation of single crystalline Ru(0001) surface with molecular oxygen. One of the reasons to choose this system is because ruthenium forms only a single solid oxide, RuO2, so that the oxidation behaviour on the mesoscale is simpler than in other cases of multiple cation valency, like iron or copper.
Above temperatures of 550 K, the initial oxidation of Ru(0001) has been shown by scanning tunneling microscopy (STM) to proceed via a modified nucleation and growth mechanism. However, closer inspection of the available STM images in the literature reveals the presence of unknown surface components that seem to coexist with the established RuO2(110) phase, rendering the oxidation of the Ru(0001) system more complex than frequently anticipated.
The researchers used a combination of I(V)-LEEM and micro.difraction analysis to identify emerging ruthenium oxide phases as the (110), (100), and (101) orientations of RuO2. By comparing to ab initio calculations of electron scattering from crystalline surfaces, the pronounced differences found in the I(V)-LEEM curves at very low energies were traced back to the unoccupied electronic structure of the differently oriented RuO2 crystallites. This correspondence allows to follow the nucleation, growth and coalescence of different faces of the same nanocrystalline oxide in real-time.
Most importantly, this methodology also enables real-time kinetic studies of dynamic processes in complex catalytic materials under reaction conditions.
Author: César Tomé López is a science writer and the editor of Mapping Ignorance.
References
- Jan Ingo Flege, Benjamin Herd, Jan Goritzka, Herbert Over, Eugene E. Krasovskii, and Jens Falta (2015) Nanoscale Origin of Mesoscale Roughening: Real-Time Tracking and Identification of Three Distinct Ruthenium Oxide Phases in Ruthenium Oxidation ACSNano DOI: 10.1021/acsnano.5b03393 ↩
1 comment
[…] Cómo se oxida una superficie metálica es un proceso mucho más complejo de lo que se podía suponer. El conocimiento de lo que ocurre en la llamada mesoescala puede ser muy importante para el estudio y mejora de los […]