Materials for fusion reactors that mimick the structure of nacre
At the end of 2022, researchers at Lawrence Livermore National Laboratory announced they had observed a net energy gain through nuclear fusion for the very first time. This monumental milestone toward fusion energy represents a huge leap forward in powering our homes and businesses with the carbon-neutral energy source. But converting this scientific achievement into a practical power source also requires new technologies to make a fusion-powered society a reality. New materials will be needed. A recent work 1 makes the case for tungsten heavy alloys and shows how they can be improved for use in advanced nuclear fusion reactors by mimicking the structure of nacre.
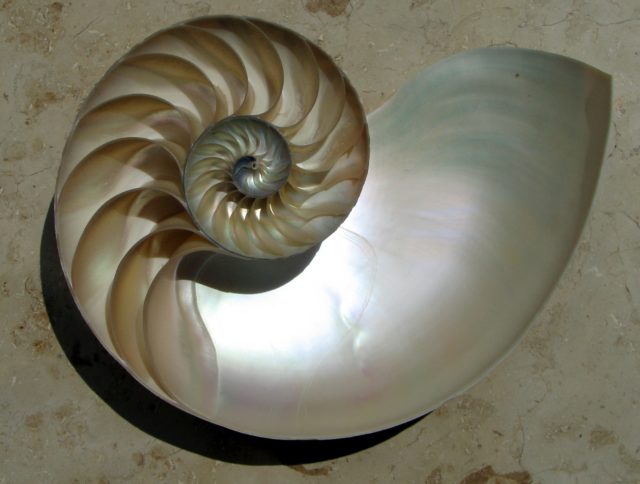
Withstanding the Heat
The Sun—with a core temperature of around 15 million degrees Celsius—is powered by nuclear fusion. Thus, it should come as no surprise that fusion reactions produce a lot of heat. Before scientists can harness fusion energy as a power source, they need to create advanced nuclear fusion reactors that can withstand high temperatures and irradiation conditions that come with fusion reactions.
Of all the elements on Earth, tungsten has one of the highest melting points. This makes it a particularly attractive material for use in fusion reactors. However, it can also be very brittle. Mixing tungsten with small amounts of other metals, such as nickel and iron, creates an alloy that is tougher than tungsten alone while retaining its high melting temperature.
It isn’t just their composition that gives these tungsten heavy alloys their properties—thermomechanical treatment of the material can alter properties like tensile strength and fracture toughness. A particular hot-rolling technique produced microstructures in tungsten heavy alloys that mimic the structure of nacre, also known as mother-of-pearl, in seashells. Nacre is known to exhibit extraordinary strength, in addition to its beautiful iridescent colors. Researchers investigated these nacre-mimicking tungsten heavy alloys for potential nuclear fusion applications.
Examining Microstructures for Major Toughness
To get a closer look at the microstructure of the alloys, the team used advanced materials characterization techniques, such as scanning transmission electron microscopy to observe atomic structure. They also mapped the nanoscale composition of the material interface using a combination of energy dispersive x-ray spectroscopy and atom probe tomography. This is the first study to observe these material interfaces at such small length scales. In doing so, some of the fundamental mechanisms which govern material toughness and durability were revealed.
Within the nacre-like structure, the tungsten heavy alloy consists of two distinct phases: a ‘hard’ phase of almost pure tungsten, and a ‘ductile’ phase containing a mixture of nickel, iron, and tungsten. The research findings suggest that the high strength of tungsten heavy alloys comes from an excellent bond between the dissimilar phases, including intimately bonded ‘hard’ and ‘ductile’ phases.
The study demonstrates how crystal structure, geometry, and chemistry contribute to strong material interfaces in tungsten heavy alloys. It also reveals mechanisms to improve material design and properties for fusion applications.
Learn more:
Materials for caging the Sun on Earth
References
- Haag, J.V., Wang, J., Kruska, K. et al. (2023) Investigation of interfacial strength in nacre-mimicking tungsten heavy alloys for nuclear fusion applications. doi: 10.1038/s41598-022-26574-4 ↩