Geopolymer, an eco-friendly concrete?
geopolymer
Author: Ada Martinelli holds a PhD in organic chemistry and is a researcher in an Italian ceramics company
The construction industry is one of the major exploiters of natural resources, and it has a great contribution to the greenhouse gas emissions and non-sustainable development of the global economy. Nowadays, it still mostly relies on concrete, which mainly contains Portland cement as the binding material. Portland cement is produced from a mixture of limestone, clay, sand and other minerals extracted from quarries. Its production process is generally divided in four different steps: at first, raw materials are crushed and ground in tube mills in order to reach small particle dimensions. After that, ground raw materials are blended together to obtain the optimal chemical composition for the cement production and the mixture is heated in a rotating kiln at about 1500 °C. Finally, the burned material is mixed with gypsum and further ground to obtain a uniform product.
Due to this high energy-demanding production process, Portland cement is responsible for about 7% of the total CO2 emissions around the world but, at the same time, this type of material is very important for human activity on this planet. This has encouraged scientific researchers to look for alternative solutions that may reduce or remove cement from concrete.
At the present day, a fully inorganic eco-friendly material might seem a utopia and, for sure, the excellent mechanical properties and long-lasting lifetime required strongly raise the challenge. However, a promising alternative material introduced by Joseph Davidovits in 1978 has attracted the interest of the scientific community: a tridimensional aluminium silicate-based inorganic polymer that he named geopolymer.
What are geopolymers?
Geopolymers are semi-crystalline inorganic materials formed by polymerization of an alkaline reagent such as sodium silicate with a source of aluminium and silicon. These elements are, along with oxygen, the most common on Earth’s crust, therefore a wide range of materials could be employed for this purpose. One of their great advantages is that various industrial waste can be used as row materials for the production of geopolymers. Fly ash, produced by burning coal in thermoelectric power plants, and ceramic by-products are just two of the large number of materials that can be exploited for the preparation of geopolymers.
In addition, the preparation of geopolymers requires low energy consumption and a significant reduction of CO2 emission compared to the classic Portland cement. Indeed, the geopolymer formation process is quite smooth: at first, it consists on the dissolution of the aluminium silicate source into an alkaline environment. Then, the dissolved aluminium and silicon ions react to form a gel that, with the appropriate curing time, organizes itself to create a tridimensional polymer network (Figure 1). Moreover, during the geopolymer preparation process, no high temperatures are required, since the curing time requires at maximum 100 °C. On the contrary, around 1500 °C are required by classical cements production.
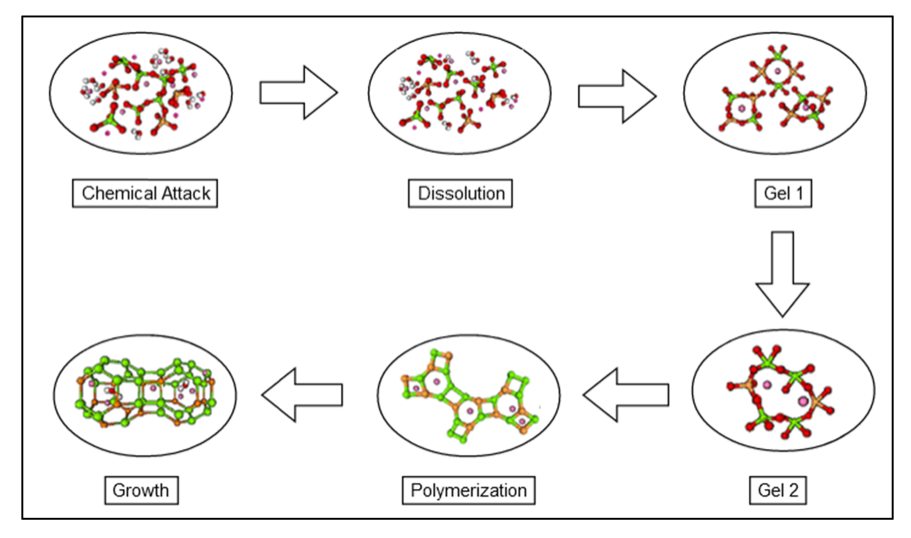
Finally, the last astonishing characteristic of geopolymers is that they can be used as inorganic matrices to formulate composite material. This property could be exploited for recycling different types of waste from industries. We all know that the management of industrial waste represents a leading global problem, thus this property could be especially exploited for the recycling of non-degradable waste.
Recently, geopolymers have attracted a lot of attention from the scientific community because of their good resistance to high temperatures, low permeability, and good compressive strength. Numerous research has been conducted in the last decades, and different geopolymer-based materials have been formulated. Given the correct formulation and preparation, geopolymeric materials have shown superior chemical and mechanical properties compared to ordinary Portland cement.
Thanks to the above-mentioned characteristic, Geopolymers are nowadays considered the most promising ecological alternative for construction materials.
A concrete example
An example of an application of geopolymer for the manufacturing of composite materials was described by Manoun and co-workers in 2022. In their work, a geopolymeric matrix mixed with ceramic sanitaryware waste was produced and characterized. Ceramic waste has been determined to have a degradation lifetime of about 4000 years due to its extreme stability and non-reactivity, which also makes it critical to find them a new purpose.
In this research, ceramics waste has been crushed and mixed with metakaolin and aqueous based alkaline activator.
Metakaolin is the source of aluminium and silicon, a mineral often used in geopolymer formulation due to its relatively high reactivity, while the alkaline activator is a solution of sodium silicate and sodium or potassium hydroxide. The alkaline activator acts in two parallel ways:
-
It dissolves aluminium and silicon contained in the metakaolin, making them available to react, forming the new geopolymer.
-
It activates the surface of the ceramic waste. Good surface activation of the ceramics waste is mandatory to have it bound with the geopolymer matrix, and therefore to achieve improved properties of the final product.
After mixing the two reactive components with the ceramic waste, the resulting slurry is cured for at least 24 hours at 60 °C and a new geopolymer-based concrete is formed.
The authors of this work investigated the influence of the size of the introduced ceramics waste. They hypothesized that an increased size could affect the performance of the final product, since the ceramic particles could act as a “wall” disturbing the formation of the tridimensional geopolymer and, therefore, the consistency of the final concrete. In this example, four different granulometric distributions were analysed (Figure 2).
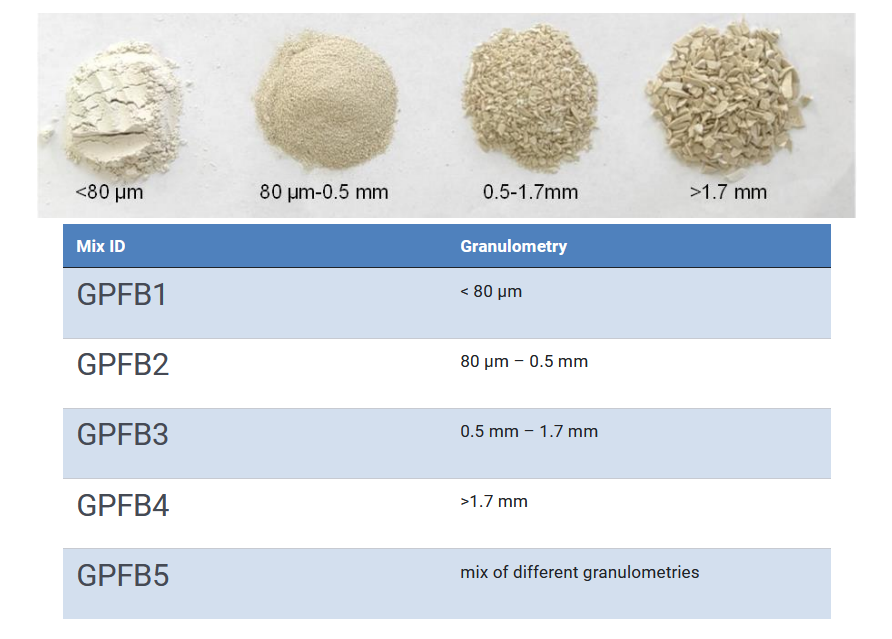
As expected thanks to the hypothesized “wall effect”, it was observed that the compressive strength of the cement was negatively affected by the increasing size of the ceramic waste (Figure 4, GPFB1 vs GPFB2-5). In addition, to a higher size corresponds a lower surface contact area of the ceramic with the geopolymeric matrix, which reduced the capacity of the two materials to interact. In facts, in order for the composite material to withstand high mechanical stress and the formation of cracks during the curing time, the geopolymer matrix and the ceramic waste have to strongly interact at the molecular level. The larger the particles’ surface area is, the stronger they can interact. It has also been observed that irregular particle shapes strongly affect the packing of the concrete, and therefore its mechanical properties. Anyways, it is worth underlining that a sharp increase in the compressive strength of the cement was observed when the ceramic waste was included in the formulation (Figure 3, GPFB0 vs GPFB1), together with a significant decrease in the overall porosity. This means that the geopolymer and the ceramic can efficiently bind, and that the latter can reduce the formation of cracks and the porosity of the composite material. Indeed, a sharp decrease of porosity has been measured in the sample composed by both geopolymer and ceramic waste (Figure 4, GPFB0 vs GPFB1).
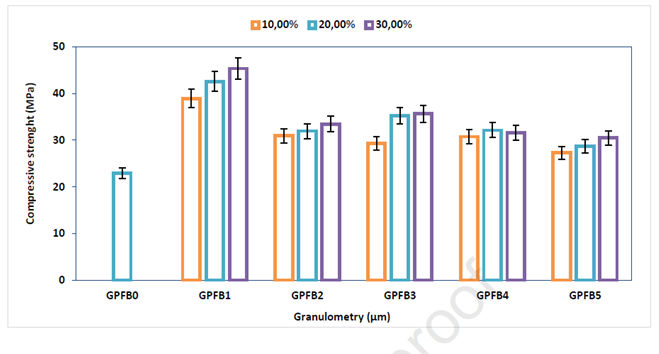
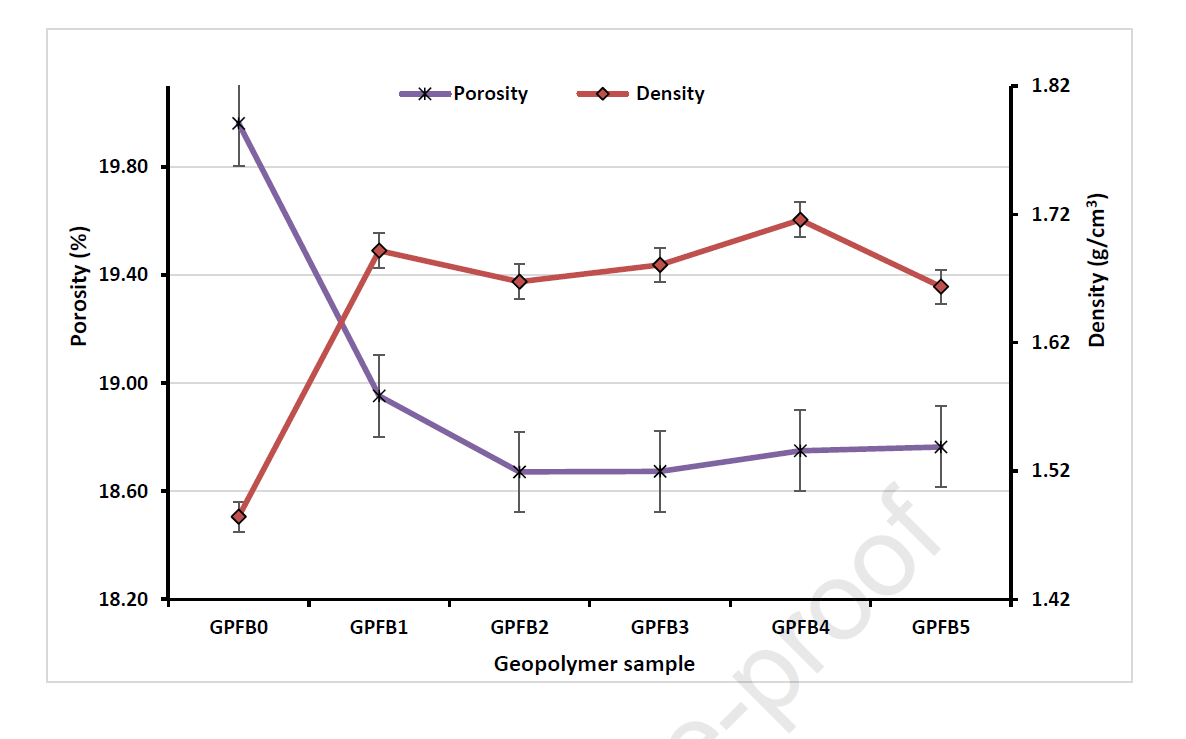
Other techniques have been applied to characterize the developed materials, all revealing that the developed geopolymer-based concrete possesses higher performances compared to conventional concretes. This is one of the numerous examples of the promising application of geopolymers to demonstrate that they could represent a greener alternative in the future of the construction industry.
At the present time, there are some example of commercialized geopolymer-based materials, but further investigation needs to be performed, especially to translate the geopolymer technology to the large industrial scale. Working and developing such alternatives is walking down a path directed toward a sustainable construction industry, hence, to answer our initial question, eco-friendly concrete could not be a contradiction any more.
References
1 D. Allaoui, M. Nadi, F. Hattani, H. Majdoubi, Y. Haddaji, S.Mansouri, M.Oumam, H.Hannache, B.Manoun (2022) Ceramics International doi: 10.1016/j.ceramint.2022.08.068
2 H. Castillo, H. Collado, T. Droguett, M. Vesely, P. Garrido, S.Palma (2022) State of the art of geopolymers: A review e-Polymers doi: 10.1515/epoly-2022-0015
3 F. M. Lea, T.O. Mason, “cement“. Encyclopedia Britannica
More on the subject:
Concrete production sustainability: the case for belite cements
A patchy model of the activation of cement