Concrete production sustainability: the case for belite cements
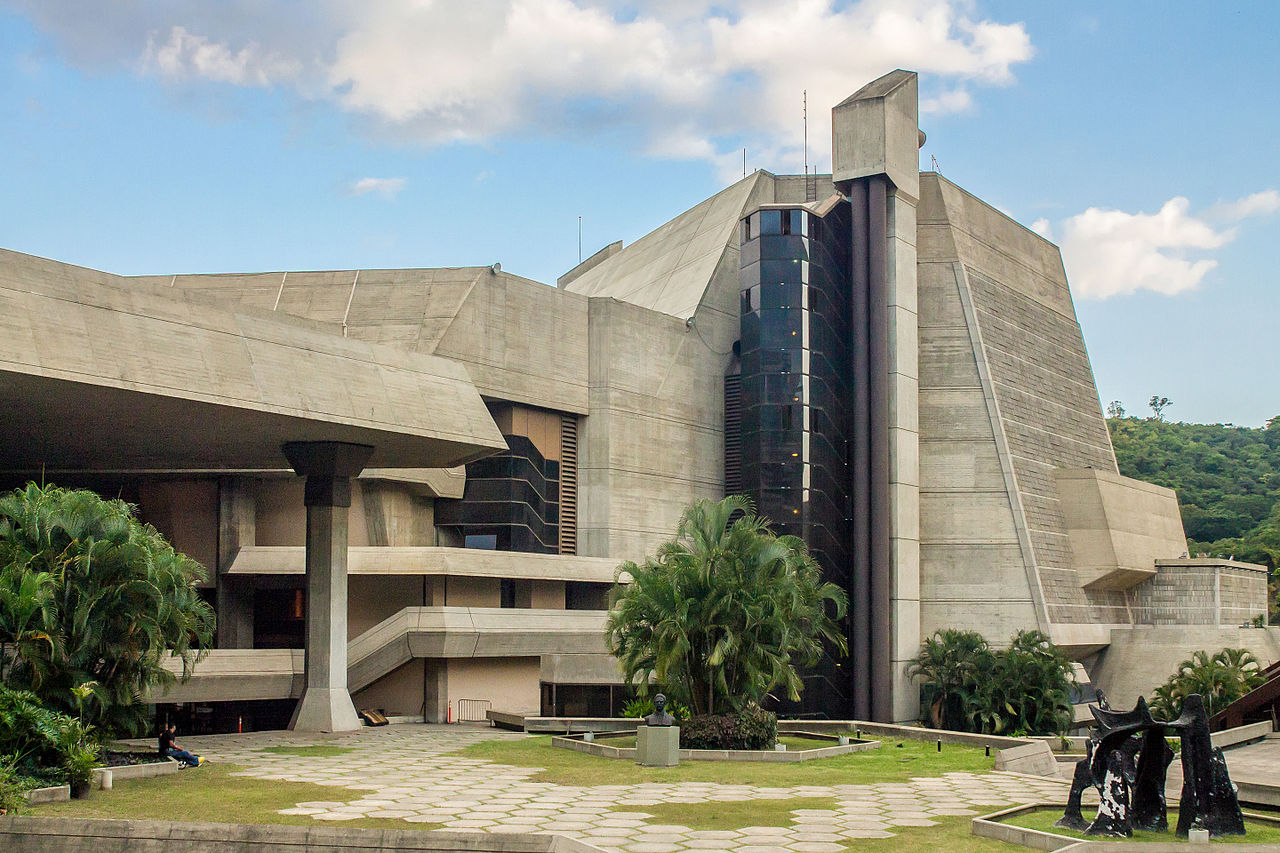
A cement is any of various substances used for bonding or setting to a hard material. A popular one, Portland cement, is a mixture of calcium silicates and aluminates made by heating limestone (CaCO3) with clay (that contains aluminosilicates) in a kiln. The product is then ground to a fine powder. When Portland cement is mixed with water it sets in a few hours and then hardens over a longer period of time due to the formation of hydrated aluminates and silicates.
The hydration process is, thus, so important that some processes have been developed in order to activate cement, i.e., to enhance the early hydration rate. The hydration phase produces C-S-H gel. Cement properties (strength, durability…) will depend of C-S-H gel structure and composition.
Portland cement is both the main product for the fabrication of mortars and concretes in the building industry and responsible of circa 7% of the total anthropogenic CO2 emissions. World production is currently ~4 Gt/year and expected to be somewhere between 4 and 8 Gt/year by 2100. On average, for every ton of Portland clinker produced, ~0.87 CO2 tones are released to the atmosphere, including emissions from limestone decomposition and burning fuel.
Producing infrastructures with longer service life would certainly contribute to an overall smaller CO2 footprint, as less cement will be needed, and it would also reduce the future production of concrete demolition waste, another environmental hazard. Concrete, made from Portland cement, water, aggregates (sand, natural gravel, or crushed stone), additions and admixtures, is the most manufactured product in the world, 2.3 per person per year: that means 7 km3 per year.
Concrete production sustainability has to be framed within the cement industry perspective. Codes of practice and cement standards must be taken into account as this industry should ensure very long service lives, at least larger than a century. Materials availability, transportation and production costs are also critically important. Hence, the approach of radically changing cement chemistry faces tremendous challenges for worldwide adoption mainly because it could go against codes of practice, or imply the use of scarce or expensive raw materials.
One way to make compatible codes of practice with fabricating concretes with likely longer service lives and (slightly) lower CO2 footprints is using cements with main components similar to those of Portland cement, but with lower limestone demand: the so-called belite cements.
Now, Ana Cuesta and Miguel Aranda (both from Universidad de Málaga) and Andrés Ayuela (CFM & DIPC) review 1 recent developments of C–S–H gel-based belite cements.
Commercial Portland cements are fabricated from clinker, obtained at 1450–1500 ºC, grinded with the setting regulator and in many cases with inorganic additions. Alite and belite, the two main clinker phases, are calcium silicate solid solutions based on Ca3SiO5 (tricalcium silicate, simplified C3S) and Ca2SiO4 (dicalcium silicate, simplified C2S), respectively. A typical grey Portland clinker mineralogical composition is close to 65 % in weight of alite versus a 10% of belite. One way to decrease the cement environmental CO2 footprint, due to a lower limestone demand, and to increase its durability is to replace most of alite with belite.
A lower energy demand and a lower kiln operating temperature, which means lowering CO2 and NOx emissions from fuel burning, are additional advantages of belite cements. A lower temperature increase at early-age hydration phase is also worth mentioning.
However, the authors find, early-age strength developments are not competitive with those of Portland cements. Hence, it is necessary to investigate novel ways of activating belite cements. This enhancement can be attained by three compatible approaches: chemical, physical; and admixture activations.
The researchers also review the current research status of activation: cost-effective element substitutions to stabilize high-temperature forms; fast cooling, milling and mild temperature hydration as physical activation; and the use of C–S–H seeds as admixture activation.
The estimated world concrete stock is 315 Gt which currently results in 0.3 Gt/year of concrete demolition waste . A new model predicts a hundredfold increase of this waste to 20–40 Gt/yr by 2100. Interestingly, the authors find that neither standard belite cements nor active ones have been researched for incorporating construction and demolition wastes. The high C–S–H gel content and its dense microstructures make belite cements good candidates for incorporating recycled aggregates, something that would also reduce their environmental impact.
Author: César Tomé López is a science writer and the editor of Mapping Ignorance
Disclaimer: Parts of this article may be copied verbatim or almost verbatim from the referenced research papers.
References
- Ana Cuesta, Andres Ayuela, Miguel A.G. Aranda (2021) Belite cements and their activation Cement and Concrete Research doi: 10.1016/j.cemconres.2020.106319 ↩