Catechol derivatives from “ideal lignin”
In the transition from a petrol-based society to a one based on bio-renewable resources, the replacement of aromatic chemicals is one of the most challenging issues. Nowadays, around 40% of the bulk chemicals belong to the aromatic category, and a myriad of products are derived from benzene, toluene and xylene. Aromatic molecules are present in plants, but in most cases at low concentrations, which makes their extraction and use in industry unviable. There are a few exceptions, such as the cardanol derived from cashew nut shell oil or the tannins, and these are already used in industry. However, their abundance is not large enough to replace all petrol derived aromatic compounds. There is though a large stock of aromatics in lignin, the polymer that confers support and toughness to plants. But precisely because of its role in nature (support and protection) lignin is recalcitrant: it is difficult to break this polymer into its individual constituents. That is why, currently, the paper industry uses it for fuel instead of converting it to chemicals.
Lignin consists mainly of two phenylpropanoid units: guaiacyl (G) and syringyl (S) (Figure 1), which are linked together as a result of radical coupling. Because of its random mechanism, the polymerization results in different types of linkages between the units and produces a complex and heterogeneous structure. The depolymerization of lignin is based on the cleavage of β-O-4 bond linkage, which accounts for 45 to 85% of all the interunit linkages. However, other linkages remain uncleaved, and moreover, the depolymerization conditions often trigger the repolymerization (condensation) of the cleaved fragments. As a consequence, the depolymerization of lignin results in several products in the best case, but it can be dozens or even hundreds (Figure 1).
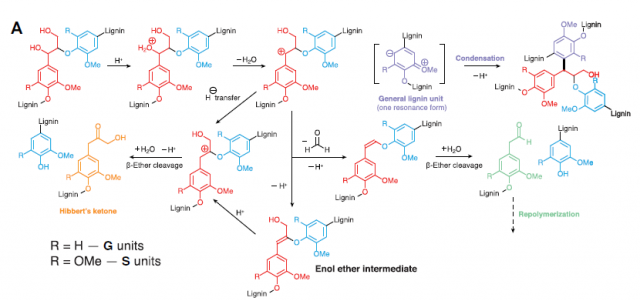
The heterogeneity of lignin is the biggest hurdle for its depolymerization. In order to circumvent this problem, researchers have bioengineered biomass to achieve more homogeneous lignins. For example, a 78% monomer yield was obtained from a modified lignin with 98% S units and around 90% of β-O-4 linkages. But what would be the outcome of an homogenous lignin, an “ideal lignin”? The answer to that question has been recently publishedi based on the studies on the depolymerization of catechyl lignin (C-lignin), an unusual type of lignin found in the seed coats of vanilla. This lignin is a homopolymer of C units, which results in benzodioxane units in the polymer (Figure 2)
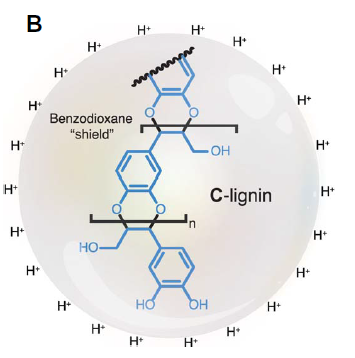
This special feature of C-lignin, lacking eliminable benzylic hydroxyl groups, makes it resistant to acidic conditions. These are typically used to purify lignin from polysaccharides, but in common lignins, where eliminable benzylic hydroxyl groups are present, the acidic media triggers the repolymerization (Figure 1). The researchers found that the acidic treatment of this lignin led to no obvious structural change in its structure. Moreover, alkaline oxidative methods, commonly used to depolymerize standard lignin, were also ineffective against C-lignin. Again, the stability of the benzodioxane structure was the reason. The authors chose the hydrogenolysis method to depolymerize lignin and compared the results with the cleavage of the model compound D1 (Figure 3, right). In both cases, two main products were observed by gas chromatography with flame ionization detection (GC-FID): Catechylpropanol (M1), catechylpropane (M2) and a minor product M3, a cyclization product from M1 (Figure 3).
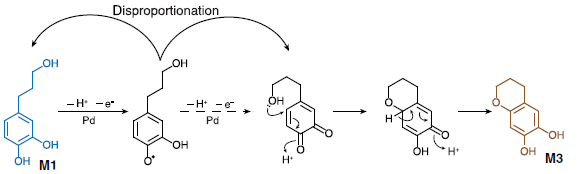
When they studied the effect of hydrogenolysis conditions on the monomer yield they were not surprised to see that the catalyst and solvent played a key role in the outcome. Methanol was the best solvent, with ethereal solvents (dioxane, THF) giving a lower yield. Regarding the catalyst Pd/C and Ru/C showed better product selectivity, whereas Pt/C displayed higher reactivity. Interestingly, palladium and ruthenium gave opposite selectivity for the main monomer: Pd/C produced catechylpropanol monomer M1 with 89% selectivity while Ru/C catalyst yielded the catechylpropane monomer M2 with 74% selectivity (Figure 4).
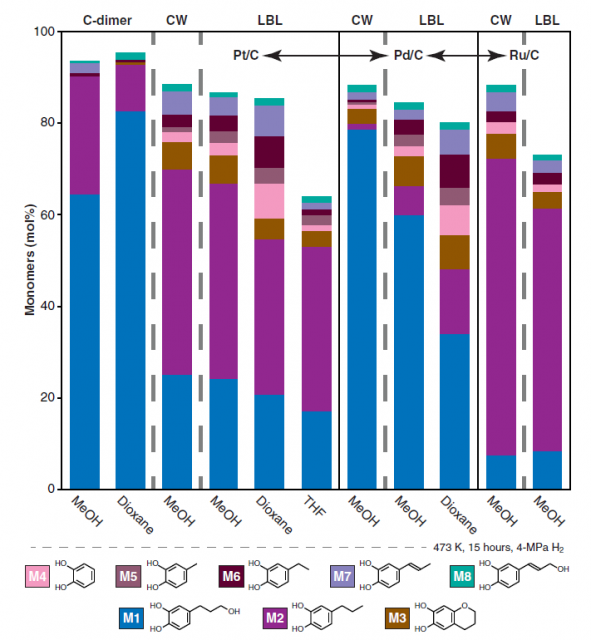
The resulting product after lignin depolymerization was analyzed and no residual polymer, neither side reactions or condensation products were detected. Based on these results the researchers could conclude that all the C-lignin was depolymerized to the monomers by the hydrogenolysis depolymerization.
The monomers that can be obtained by the depolymerization of this type of lignin are highly interesting because they have the catechol core. Although compounds M1 and M2 are not currently used in bulk by the chemical industry, catechol is an important commodity chemical, as it serves as the precursor for pesticides and in the fine chemical industry (fragrances, flavors, drugs). For example, vanillin, the aroma of vanilla, is currently synthesized from catechol, which in turn is produced from phenol, and this derives from benzene. If petrol is to be replaced by biobased resources, catechol derivatives could come from C-lignin. Unfortunately, C-lignin is a rather unusual lignin. Authors speculate that this could be circumvented if C-lignin could be produced in energy crops. However, this is a big question mark, as it is not known if plantation trees such as pines or poplars could tolerate the genetic modifications needed to make them produce C-lignin. A more feasible approach could be to use candlenut shells. They are abundant as a by-product of the use of the nuts for biodiesel and have been reported to give catechols upon depolymerization.ii
References:
iY. Li et al. Sci Adv. 2018;4:eaau2968. doi: 10.1126/sciadv.aau2968
iiK. Barta et al. Green Chem. 2014, 16, 191–196. Doi: 10.1039/C3GC41184B
2 comments
[…] Petrolioa albo batera uztearen arazoetariko bat ez da hartatik datozen erregaiekin dabiltzan garraioetan izango duen eragina edota elektrizitatea ekoizteko orduan sorrarazi ditzakeenak. Petrolioan oinarritutako material ugarien ekoizpenean nabarituko da ondorioa. Hala ere, petrolioaren ordezkoak aurki daitezke gutxien espero ditugun […]
[…] se basan en él. Y se pueden encontrar sustitutos en los lugares más insospechados: Catechol derivatives from “ideal lignin” por Pablo […]