Biogasoline production and integration into current petrorefinery process
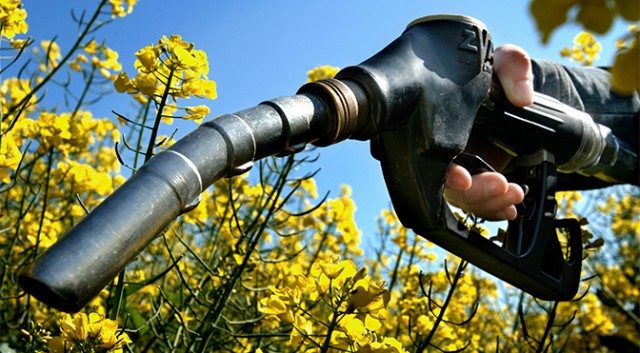
Planes, ships, trucks and (most) cars run on different fractions of crude oil, composed of carbon chains of different length: Diesel (C10-C22), kerosene (C8-C16) and gasoline (C5-C12). Despite their current supremacy, it is well known that fossil fuels will not be the energy source of the future: In the long term because of their depletion, and in the nearer term due to government policies. The advances in the use of renewable energies are encouraging, but these technologies are not mature yet to completely replace fossil fuels. Consequently, the European Union has set a short term goal of 10% biofuel use in transportation by 2020. Currently, blending bio-based ethanol with fossil-derived gasoline is the most common option, and the E10 label that one can see in tanking stations stands for it. However, up to now, ethanol is produced from fermentation of edible carbohydrate resources, which is called first generation biorefinery (Figure 1). Although second-generation refineries should solve this problem, they require three times higher investment cost.
In a previous article, the full utilization of lignocellulose was discussed. Lignocellulose is the structural material present in the cell wall of woody plants, composed of aromatic (lignin) and carbohydrate (cellulose and hemicelluloses) polymers. Currently, only the cellulose fraction is used, while hemicelluloses and lignin are treated as side-products or used for low-value applications. There has been extensive research into the conversion of (hemi)cellulose to alkanes, and among them, gasification and pyrolysis/liquefaction are the most promising methods. However, they yield a great diversity of hydrocarbons as well as other products, which hamper its direct use in current biorefineries. Now, a group of researchers report a two-phase catalytic slurry process that converts (hemic)cellulosic pulp into light naphtha (Figure 1). 1
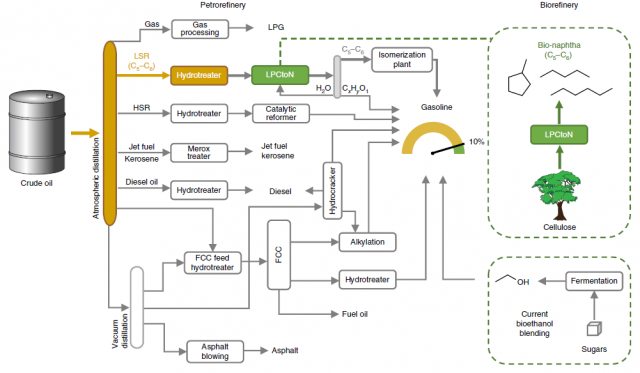
In a typical petrorefinery setup the crude is distilled into different fractions, one of which is the so-called light straight run naphtha (LSR) which comprises alkanes of 5 or 6 carbon units (C5-C6). This stream is then isomerized into branched alkanes to increase the gasoline octane number. The authors propose to directly enrich the present LSR with the bio-naphtha derived from cellulose (LPCtoN, Figure 1).
In order to convert the cellulose to naphtha, the researchers propose a biphasic catalytic system. The aqueous phase contains a soluble heteropolyacid which leads to sugar hydrolysis and dehydration (for example, to 5-hydroxymethylfurfural). The organic phase contains a redox catalyst (polyacid–modified ruthenium on carbon), which performs dehydration/hydrogenation to alkanes. Both phases are stirred in a slurry reactor at 493K under 5MPa of hydrogen atmosphere. They envisioned that the use of LSR as the organic phase would be ideal, and for that, they studied the behaviour of their system using petrol (mainly C7 alkanes) and petroleum ether (C6 alkanes) as solvents. Especially the latter resembles the typical LSR before the isomerization step. When they loaded their biphasic reactor with a naphtha/water ratio of 25:75 containing 7 weight % of cellulose in water, complete conversion to alkanes was achieved, with an efficiency of 68% for petrol 76% for petroleum ether. (Figure 2) This corresponds to a 10% of biomass enrichment of the LSR. The effect of the chain length was further studied with other alkane solvents from C7 to C16, and it was observed that the shorter the chain, the higher the yield.
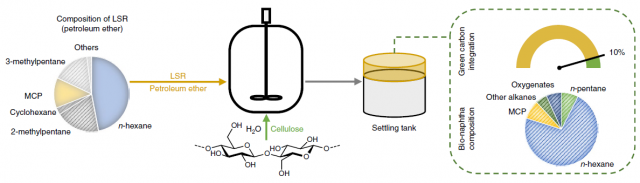
For the success of the conversion, it is crucial that both phases are compartmentalized, as the hydrolysis and dehydration must take place in the aqueous phase before the hydrodeoxygenation in the organic phase. Having said that, the oxygenated intermediates formed in the first reaction must transfer from the aqueous to the organic phase, where they are scarcely soluble. At elevated temperatures, though, the extraction of these intermediates can take place, and shorter chain alkanes help the process by increasing the polarity of the organic phase (Figure 3). By changing the organic phase solvent and the water/organic phase ratio the system can be tuned to increase the bio-carbon enrichment. The highest value achieved was 20%, by using a 12.5:87.5 water to petrol ratio, starting with a cellulose loading of 9 weight %. This was also the limit, as at this loading the hydrodeoxygenation efficiency reaches its top.
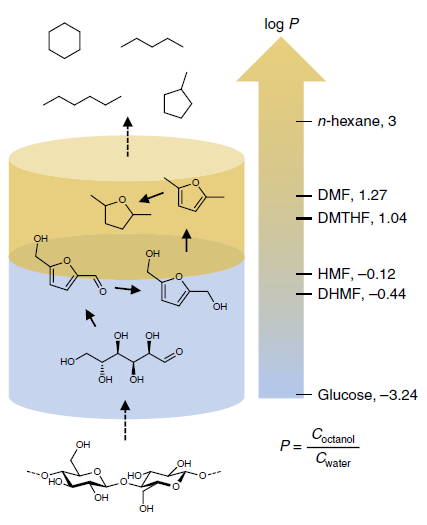
Importantly, the authors did not limit their studies to pure cellulose and used real feedstock. They had previously developed a reductive catalytic fractionation process to extract lignin oil from lignocelluloses. Birch wood was processed by this method to yield impure (hemi)cellulose pulp (figure 4). This pulp was submitted to the LPCtoN process using petrol as the organic solvent and the efficiency to alkane conversion reached 56% (equivalent to 7% bio-based carbon enrichment)
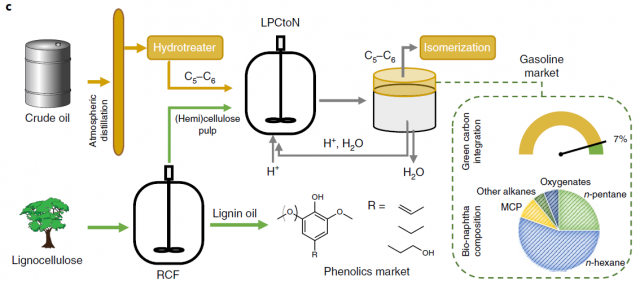
The strategy presented by the authors is very interesting from the applicability point of view. The fact that the alkanes from renewable resources are mostly indentical to the petrol-based counterparts would ease its implementation in current refineries. Moreover, their calculations show that the LPCtoN process would be feasible in terms of logistics. Nevertheless, the high loading of catalyst is an important drawback, as well as the small scale of the experiments. Although the authors do not comment on these points their future work will hopefully target these issues.
References
- B. F. Sels. et al. (2018) Direct upstream integration of biogasoline production into current light straight run naphtha petrorefinery processes Nat. Energy doi:10.1038/s41560-018-0245-6 ↩