The 3D-printing hype: expectations vs. reality
After years of watching manufacturing plants relocating offshore, hundreds of thousands of jobs gone and deindustrialization creeping up, policy makers and investors from high-income countries are finally willing to bring the manufacturing sector back. But they won’t get this done just competing globally for mass, low-cost production; those days are long gone. On the contrary, competitive advantage in the global market requires smart, high-tech manufacturing techniques. Experts have identified a bunch of enabling technologies that will allegedly lead us to the 4th Industrial Revolution, the so-called Industry 4.0. These technologies will enable the complete digitization of most industrial processes, and mainly include: Cognitive Computing, Cloud Computing, Cyber-physical Systems, Virtual Reality, the Internet of Things, Big Data and last but not least, 3D Printing (also called additive manufacturing).
3D printing has become so popular in the media that many talk about the “3D printing hype”, meaning that public expectations go far beyond realistic prospects. Even political leaders have been carried away by the lure of this technology. President Obama described 3D printing in his 2013 State of the Union speech1 as the technology with “the potential to revolutionize the way we make almost everything”. With such bold expectations, can we discern non-realistic prospects from really feasible advances? The Gartner Hype Cycle for 3D printing2, shown in figure 1, helps us to figure out the maturity of certain 3D printing applications. This curve (in fact, not a cycle at all) was conceived by the American IT firm Gartner as a graphic representation of the maturity of emerging technologies, and it considers five different phases over time: technology trigger, peak of inflated expectations, trough of disillusionment, slope of enlightenment and plateau of productivity.
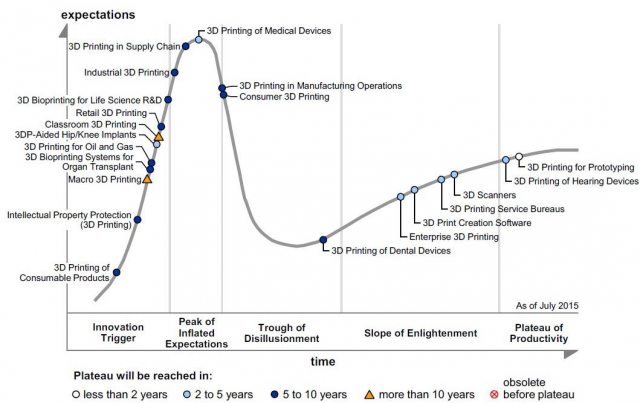
The graph above shows how far the expectations go from a realistic uptake of different 3D printing applications. We see that bio-printing of human organs, or 3D printing of large, structural parts, are still in a research state, still far from their commercialization phase. However, other applications have already reached their plateau of productivity; this is the case for rapid prototyping, where 3D printing has found one of its most useful applications so far. It allows the fabrication of scale models of physical parts, avoiding complex production processes and speeding up product development. Rapid prototyping allows designers and engineers verify their designs and perform tests before setting up a whole production line. However, this technique is far from being new, as it was already in use back in the 80’s, where we can find the first American patents of this manufacturing process under the name of Solid Freeform Fabrication.
Visionaries set the following 3D printing revolution in the additive manufacturing of metal, structural parts for aerospace applications. The aerospace sector is one of the early adopters of this production technique, and it accounts for 15% of the current revenues of the 3D printing industry. The main drivers to use 3D printed parts in aircrafts are design freedom, weight reduction and the possibility of producing one single part where a set of assembled parts were previously needed. However, these advantages don’t come without challenges. Aerospace industry is strictly regulated and needs long validating times for new components. The first 3D printed part certified by the US Federal Aviation Administration (FAA) for a commercial jet engine was approved in 2015, and it was made by GE Aviation, a company that is making huge investments in the last few years in acquiring 3D printing companies and intellectual property. The new Airbus A350 contains more than 1000 3D-printed parts, most of them non-structural, which are less demanding in terms of performance.
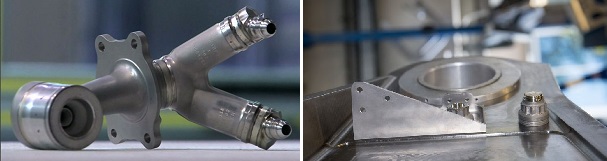
A group of researchers from the RWTH Aachen University and the Technical University of Berlin3 have recently carried out a comprehensive survey of 65 experts in additive manufacturing (41 from industry and 24 from academia) belonging to different fields and perspectives. They have been asked about the implications of 3D printing for industry, policy and society in the near future. The purpose of this study is to get a picture of the most probable scenario for the 3D printing sector in 2030. Looking at the results, we can ensure that 3D printing will be a disruptive technology, that is, it will replace traditional manufacturing techniques, and more than that, it will lead to new business models, products and value chains.
The results of this survey have been divided into Political, Economic, Socio-cultural and Technological effects of additive manufacturing (what is usually referred to as a PEST analysis). In the political arena, management of intellectual property (IP) will be a key area. 3D printing techniques will allow replications of products only based on digital files stored in the cloud. This fact will challenge intellectual property rights in the same way that other digital goods such as music, films or books did before. Experts agree that in 2030 conventional IP for digital products will be no longer useful, and novel forms will have to be in place, such as Creative Commons, sharing licenses or open source. Some even think about streaming-services for product files similar to those already in use to solve the digital dilemma in music.
From the economic perspective, it is generally agreed that 3D printing will change business models and market structures. Some currently essential parameters such as the time for a product to get to the market or the cost of product customization will be drastically reduced, and thus less critical for competitive advantage4. The additive manufacturing market will focus less on the manufacturer and more on the designer. In fact, the product itself will be the digital file, which could be later produced in any 3D printing machine with access to that file. This will lead to a more decentralized production, which will also enable local-based manufacturing close to the end user.
Nevertheless, experts believe that additive manufacturing will soon develop two different manufacturing systems: less critical parts will be produced locally, whereas critical parts will be made at specialist hubs with the necessary qualification and quality control skills. Some of these 3D Printing Hubs are already operating, and the EU is actively promoting these facilities in order to give access to small and medium enterprises that won’t be able to afford 3D printing machines of their own.
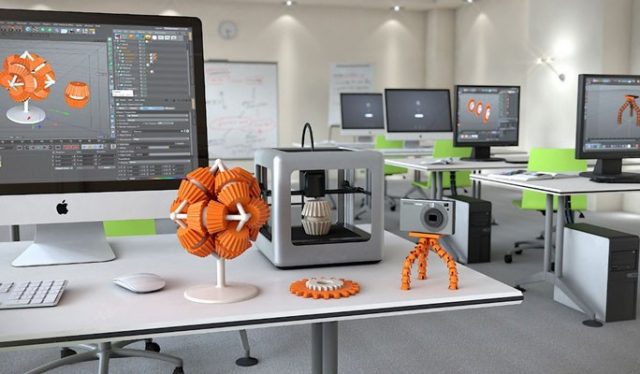
Regarding socio-cultural aspects, it is believed that 3D printing will change consumer behavior and demand, contributing to positive trends such as circularity, sustainability and zero-waste objectives. Early adopters are already accessing free product designs, or even taking part in their co-design, to print them later at home in their own 3D printing machines, giving rise to the figure of the prosumer, who is both producer and consumer. However, experts agree that this kind of figure will comprehend just a small community of tech enthusiasts, rather than becoming a mainstream behavior.
Finally, from the technological point of view, many experts mentioned that 3D printing will overcome current restrictions in manufacturing of multi-material products and embedded electronics, reducing joining and assembly operations, and broadening the range of applications. Furthermore, 3D printing will enable mass customization and individualization of products with no penalties in cost or time, as changes will only affect the digital file, not the production process (as there is no need for new tools or molds).
At the moment, 3D printing is still at an early stage in most application areas and main developments are being promoted by big equipment providers or research and technology organizations. We are probably far from seeing an immediate revolution in manufacturing, but we are indeed very close to see new regulations and policies in place to promote these changes. As with many other smart manufacturing techniques, many questions arise: will 3D printing effectively contribute to industry back-shoring? And if so, will it contribute to increase welfare and employment, or will it drastically reduce the number of employments as it is expected with many other digital techniques? All possible answers will have to be explored.
References:
3Ruth Jiang, Robin Kleer, Frank T. Piller.Predicting the future of additive manufacturing: A Delphi study on economic and societal implications of 3D printing for 2030, Technological Forecasting and Social Change, Vol. 117, 2017. doi.org/10.1016/j.techfore.2017.01.006
4C. Weller, R. Kleer, F.T. Piller. Economic implications of 3D printing: Market structure models in light of additive manufacturing revisited, Int. Journal of Production Economics, Vol. 164, 2015. doi.org/10.1016/j.ijpe.2015.02.020
3 comments
[…] Badirudi denetarik egin daitekeela 3D inprimatzearekin, etxeetatik hasi eta ilargi baseetara, kotxe atalak barne. Hala al da, baina? Silvia Romanek argitzen du: The 3D-printing hype: expectations vs. reality […]
[…] edible pizza, chocolate mousse, and dumplings. The potential seems endless, yet 3D printing hasn’t advanced as rapidly as some experts […]
[…] edible pizza, chocolate mousse, and dumplings. The potential seems endless, yet 3D printing hasn’t advanced as rapidly as some experts […]